1 品質問題の背景
クレームの語源は「大声で叫ぶ」であり、所有者が受けた損害を公衆に訴え、賠償を請求する権利の主張を表しています。特に品質クレームは製造業にとって頭の痛い問題です。ブランドイメージや受注などの企業業績に悪影響を与えるだけでなく、社内の意識を低下させる要因にもなるからです。
ただ、クレームはユーザーからの企業に対する期待であると受け止めることもできます。期待がなければクレームを出す気も起きず、期待に応えなければ、企業の明日はありません。クレームはお客様から頂いた最大の「体質改善の機会」と考えるべきではないでしょうか。
少子高齢化で人手不足が続く中、製造現場では派遣社員や外国人労働者などの非正規雇用者の割合が増加しています。それにより現場では、管理・監督力の低下とともに品質保証レベルや安全・安心の確保にどう取り組むかが重要視されています。働く人の意識や感性により、ものごとを理解するレベルは異なります。もはや「決められた作業要領と手順を守っているから大丈夫」という捉え方では、品質クレームを防止することはできません。言葉だけでは表現できない曖昧な部分をいかに伝え、クレーム防止につなげるか、その問題解決の方法論がいま切実に求められています。
2 現状の再発防止策の課題
各企業では品質問題の防止策を設けています。ところが実際のところ大変多くの課題を抱える事例が見られます。それらを集約すると次のようなケースになります。
1 再発防止のアクションが打たれていない
品質クレームに対する認識が弱く、対策すべき状況が見過ごされており、再発が避けられない状態。
2 立案した対策が実施されない
対策立案の意図が不明瞭であり、実現不可能な対策を定めているケース。口頭での連絡に終始しており、具体的なアクションプランがない。
3 実施した対策が機能していない
あまり努力を要しない対策レベルに留まっている。対策(手段)が自己目的化しており、実施後の評価等のフォローアップが不充分である。
4 本当の原因をつかめていない
三現主義(現場・現物・現状)を意識できておらず、実態把握に漏れがある。品質問題解決に関する考え方や科学的な方法論が確立していない中で、各担当が苦心している。
3 ヒューマンエラーと品質問題
人は判断ミスを犯しやすい存在です。事故の原因としてヒューマンエラーが指摘されるように、人の認知構造のしくみには勘違いや思い込みを引き起こす特性が潜んでいます。
また、組織の中で働いていると、他人まかせになっていることがよくあります。たとえば「最近、クレームが出たようだが、品質管理部門が対応するだろう」などと考えてしまう。この根底には「できるならば面倒な仕事はやりたくない」という逃げの意識が作用しています。
生産の4 M( M a n : 人、M a c h i n e : 設備、Material:原材料、Method:作業方法 )において、その主体は作業者である「人」です。いつかは故障する機械、正しい保管方法が必要な原材料、作業マニュアルの優劣は生産性や製造品質にも影響します。これらの要素には各々が抱える課題があり、ヒューマンエラーとの関連も深くなっています。
現場における作業者についても、その意識レベルは時々刻々と変化しています(図1)。長時間の疲労により集中力は低下し、作業の慣れは注意力の欠如を引き起こします。その意識レベルにより、勘違いや錯覚、モノ忘れなどが日常的に発生しているのが実情です。錯視図形で確認できるように、思い込みにより私たちの脳は容易に騙されてしまいます。つまりヒューマンエラーは避けられない人間の特性であり、品質問題防止とも密接な関係を持つテーマです。
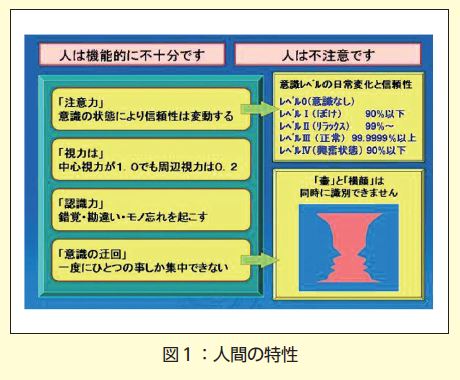
4 問題解決手法について
問題解決のため、幾多の科学的な方法論が語られてきました。たとえばリスク管理の考え方を示すものとして「スイスチーズモデル」があります。チーズには多くの穴が開いているのですが、互いに穴の位置が異なる複数のチーズを重ねることで貫通する可能性を低くできます。ミス防止の確認作業も一人ではなく、複数の眼でチェックすれば飛躍的に精度が高まります。それぞれの異なる視点で見逃しを防止できるからです。
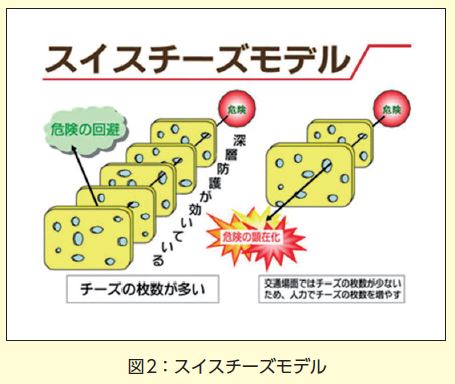
一方、現場でよく使われる問題発見手法として「なぜなぜ分析」があります。品質不良の原因を繰り返し根源に遡りながら突き詰めていく手法ですが、実施者の力量や経験に頼る部分が多く、時間がかかるわりには原因追究が不十分になり真因がつかめないという傾向がみられます。
他にも、論理的につながりを調べるモデルとして「FT図(フォルトツリー:故障の木)」があります。これは要素ごとのエラー発生率を加算して、着目している事象が起こりうる確率を算出する科学的な手法です。ただ、一般的にはFT図が使われる範囲は限られているのが実情です。
このように問題解決手法は様々ですが、あまり煩雑になりすぎては使うことが出来ません。品質問題はシンプルに考えることが必要ではないでしょうか。次に私自身が経験により編み出した品質問題の解決手法について述べたいと思います。
5 問題の発生プロセスを捉える「いきさつ(経緯)分析」
「いきさつ(経緯)分析」では、正常な状態から、いきなり問題が発生することはないと考えます。問題になる前に「不具合な現象」が発生しているが、見過ごされている場合が多いのです。その「不具合な現象」の要因(原因)となっている事を「問題のタネ」とネーミングしています。
「問題のタネ」という呼び名は、多くの業界で現場の第一線の方やリーダーの方々に色々と意見をお聞きしたなかで、問題発見のイメージが沸きやすい呼び方として名づけたものです。品質問題の解決に向けては、問題のタネ(正常な状態から問題に変化したポイント)を発見することが大切です。
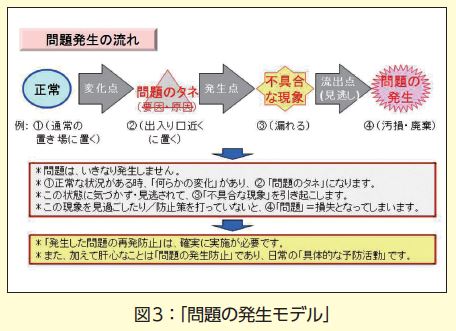
問題のタネに気づく方法は、現場で感じる「○○しにくい/××しやすい」を探すことです。
たとえば「見えにくい」「判りにくい」「やりにくい」「間違えやすい」「失敗しやすい」「忘れやすい」ところはどこか。このような問いかけをすることで「問題のタネ」が目前の現実として気づけます。
そして、各職場で見過ごされている「問題のタネ」の対策を考えることを「予防活動」と呼んでいます。潜在的な「問題のタネ」を減らすことが「予防活動」であり、図5左側の上部が「ハインリッヒの法則(1:29:300)を示しています。そして下側にある3000件の部分が見えない「問題のタネ」です。品質問題につながる不安全行動や不安全行為は、なかなか気づく事ができず、見過ごされているものです。また、気づいていても具体的な回避のための対策が打たれず、災害やヒヤリハットにより顕在化する傾向があります。コンサルティングの現場では「問題のタネに気づこう!」という呼びかけをして、第一線の皆さんに「予防活動」に取り組んでいただいております。
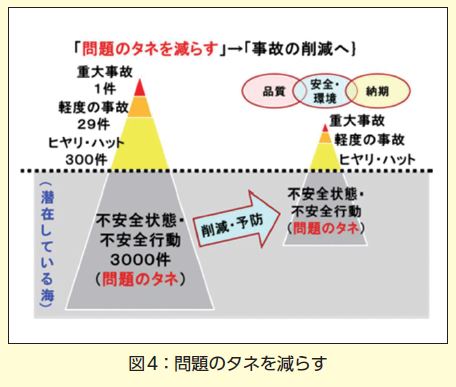
6 問題のとり上げ方トレーニング
品質問題の発生を避ける「予防活動」を推進するには「問題のタネ」や「不具合な現象」をとらえることが大切です。ところが問題を発見すると、それらを検討することなく、あてずっぽうで対策を実施してしまうケースがよくあります。これでは根本的な「予防活動」は出来ません。
大切なことは、「問題のタネ」「不具合な現象」「問題」という3つを明確に区別することです。こうした区分の実践を積み上げることが職場内の問題解析力と解決力の向上につながります。まずはやさしい身近な問題からトレーニングしていきましょう。
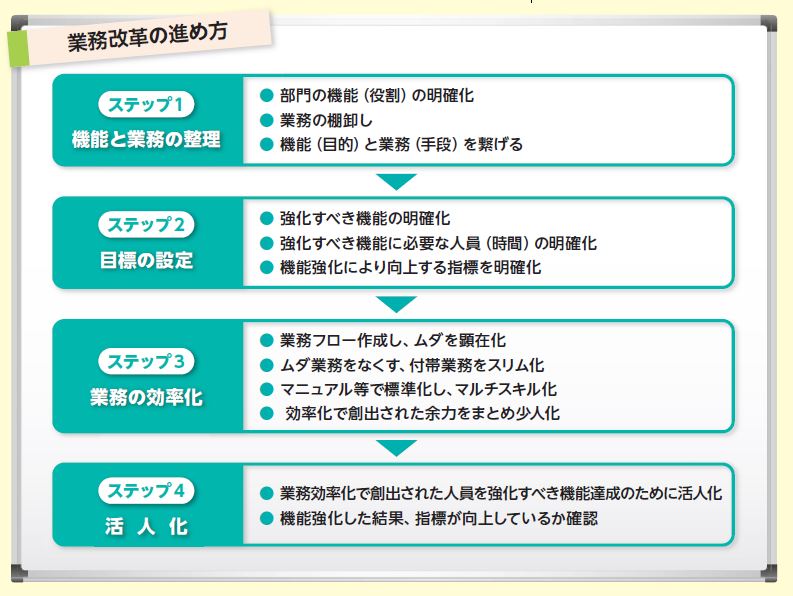