多品種少量や受注生産が主流となったモノづくり、その根幹を担う設計開発部門でのトラブルやミスが増えている。発生する不具合や問題の後処理に工数をとられて、本来の品質とコストを両立させる設計開発プロセスの仕組みそのものが衰退していることに危機感が感じられる。営業~設計~製造と部門間の連携がとれず、仕様不明確、トラブル発生、納期遅延、目標コスト未達の負のスパイラルに陥っている企業が多くなっている。
過去からのやり方の延長線上で業務を続けていては、改革は難しく負のスパイラルから脱却することは出来ない。
かつて、アジアや発展途上国の設計者たちは、「日本に学べ!日本に追い着け」ということで頑張ってきた。いつの間にか日本には追い越されている分野も増えている。
日本では、設計者は属人化された固有技術はあるが、個人の技術にとどまり組織の技術と知恵になっていないことが多い。設計水準を体系的に強化する仕組みがなきに等しい。「何かあれば聞いてこい」「トラブル発生後に対策を考える」と言ったQCD(Q:品質 C:コスト D:納期)の問題究明が後回しにされた環境で本当に優秀な設計人材が育つのだろうか。
組織の技術を成長させる設計の仕組み・仕掛け、これがないと伸びない。期待する人材が育たない。だから、トップが主導する設計開発を基軸にした最上流の営業・設計~下流の製造まで全社を巻き込んだ抜本的改革が今必要である。
設計品質&コスト両立の抜本的改革の進め方
どうすれば抜本的な改革ができるのか。実際の事例からそのポイントを紹介したい。
A 社「 設計~製造のコンカレントエンジニアリング QCDのつくり込み」
■ 抱えていた課題
電機関連装置を製造するA社のある部門は、新製品開発の手戻りが多く、開発日程の遅れと目標コスト未達の日常的な慢性化により危機的な経営状況にあった。営業企画→生産技術→製造と直列的に仕事が進められ、情報とモノが流れる運営により、すべての設計出図の完了後にデザインレビューが実施される状態であった。その結果、後工程の生産技術・製造段階で問題が発生し非常に大きな手戻りになっていた。
A社では、設計出図を待って、生産技術、製造が工程設計や製造方法を検討する姿勢であり、実際にやってみないとわからないという感覚も意識としてあった。実際にモノを試作して検証する流れで進めていたため、新製品開発の立ち上げに計画の1.5~2倍の時間を要し、トラブルが慢性化し、設計変更も多く、利益と納期未達となる負のスパイラルが常態化していた。
設計・生産技術・製造の各部門間の壁がいつの間にか厚くなり他責に対する批判が多く現れていた。業績が低迷すると、どうしても他人や他部門に対する責任押しつけの意見が上がりやすくなる。これはどの会社も共通していると思う。
■ 改革の進め方
改革のポイントはフロントローディングとコンカレントエンジニアリング。この二つの切り口でシステム構築を推進した。構想設計の段階で要求品質に対する設計特性、機能とコスト及び達成手段となる機構展開の追求を体系的に進める。この段階で営業・設計・品証・生技・製造部門の協働により、最上流の段階で中身の濃い構想設計と仕様検討のための活発なデザインレビューが実施できる仕組みづくりを展開した。
詳細設計においても、全部を出図して渡すのではではなく、ブロック単位の分割出図をもとに設計~製造の各部門との3次元データによるデザインレビューを実施した後で出図する流れを完成させ、ほぼ手戻りが発生しない仕組みが構築できた。
良い影響として、設計部門では機能とコスト視点から構想設計が進められ、生産技術・製造部門からは加工性・組立性を考慮した製造し易い形状やコストダウンの提案、品証からはクレーム未然防止の提案等、部門間での情報共有化を通じたデザインレビューが推進できるようになったこと。そして、設計と関連部門との壁が依然と比べ格段に低くなり、活発な意見交換により新製品の垂直立ち上げに関するノウハウが蓄積されるようになったことが挙げられる。
この改革は、製造工程を熟知していない設計技術者に新たな視点や知恵を提供し、関連部門連携強化のデザインレビューにより各部門が自責で課題解決に取り組むという動機付け効果が働き、モチベーションアップとやる気を引き出すプラスのスパイラルアップに変化していった。
目標品質・目標納期・目標コスト達成率の3つの指標が年々向上し、目標をクリアーできた案件も増加している。新製品開発の体質強化により人材育成とQCDを造り込んでいく仕組みの定着化が進んでいる。今後、未来へ向けて大きく飛躍することが期待できる。
B 社「 モジュール化推進と機能価値設計による 短納期と利益率の大幅な改革」
■ 抱えていた課題
B社は産業機器プラント関連装置を製造するトップメーカーである。近年、受注生産を中心に売上は伸びていたが利益が圧迫されていた。
営業担当者は、顧客の要求情報を丸のみする御用聞き型の営業スタイルであり、提案や確認不足により部分的な仕様漏れや顧客からの仕様追加が発生、納期遅延と利益率低下が続いていた。
設計部門では、受注生産での顧客仕様の対応のため、微妙に異なる類似部品の設計や必要性のない新図が増加、手戻りが慢性化していた。属人化された設計体質の影響もあり、部品の種類や目標コストがオーバーする後追い対策型となっていた。
同一機能部品でも数ミリ違いの類似図面を無数に抱える企業は多いが、B社もそれに該当していた。部品の種類が増えると製造の過剰負荷により外注比率が多くなる。納期優先のため調達購買コストの最適化を検討する時間がなく、かつ外注納期遵守率も悪化していた。
現在の延長線上で何かを解決しようとするのではなく、やり方そのものの変更が必要であった。
■ 改革の進め方
改革の第1のカギは“モジュール化”設計の推進である。経営方針として、モジュール仕様とオプション仕様の割合を数値目標に設定した。部品の標準化、共通化という視点ではなく、機能別ユニット構成とし、サブユニット単位でもモジュール化を推進した。そして、顧客の要求仕様と機能別ユニットの紐付けが容易に実施できるシステム構築によりモジュール仕様の運用率を高めていった。
営業部門は、顧客要求仕様に一致するモジュール機能ユニットを選択する仕組みに変化させていった。登録されたモジュール標準仕様に導く提案型と顧客オプション仕様を含めて改革を進めた。設計部門では、基本的にオプション仕様部分の設計に集中できるようになり、製造部門では、モジュール仕様部分は出図納期を待たずに進めることができ、部品種類の削減効果は製造部門の生産性向上と調達購買費のコストダウンにもつながった。
モジュール化は納期短縮とコストダウンには一定の効果を発揮するが、モジュール自体にムダが含まれている場合は目標コストが未達となり利益率の獲得は難しい。
外部環境の変化が激しい現在では、モジュール部分及びオプション部分の品質とコストの見直しが必須条件である。日々高まる高品質・低コスト・短納期要求に対応し勝ち続けるためには、もう一歩踏み込んだ新たな視点での改革が必要であった。
改革の第2のカギは“品質とコストを両立させる機能価値設計”の推進であった。
顧客要求仕様と魅力品質の評価等から機能とコストの展開を実施し、これらを具現化するための機構手段を検討した。多くの設計者は機能ユニットの目標性能のみを自己流で検討し、設計後にコストオ-バーになる傾向がある。設計性能には関心があるがコストには無関心な傾向が強いのが設計者の特性であり、B社でもそうであった。
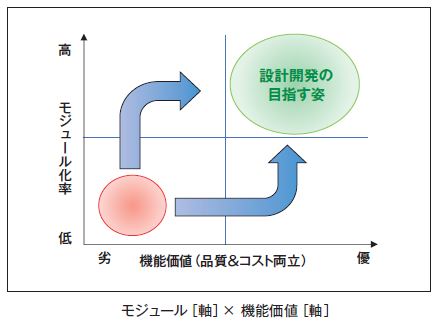
機能価値設計の基本的考え方を一言でいえば、機構・構造といった見えるモノの価値を観て重要度を判断するのではなく、機能である役割の重要性を観て価値を判断することである。B社では、この考え方を基本ベースに新たな視点でアイデアを創出し、現状モジュールやオプション部分の品質とコスト面を見直し更なる改定を加えていった。改定という考え方で新たな原則や種類を増やさない方針で進めるのがコツである。
第1軸と第2軸は自社の弱点に合わせた進め方を選択して進めることが多く、B社では第1軸→第2軸とステップを踏んで進めた結果、現在では、設計開発のQCDを進化させる体質強化力が向上してきている。
B社ではトップ主導のもと1年目、2年目と対象領域を段階的に拡大しながら進めてきた。成功体験を積みながら徐々に広げていく。設計開発の抜本的プロセス改革は、長期的な視野で自社の製品特性に合わせたノウハウを熟成させていくことが成功の秘訣である。このような取組みの結果、設計者は本来の付加価値を上げる品質とコスト両立の設計に集中ができ、B社では5年間の活動を通じて目標となるQCDの達成度は格段に向上し、永続可能な仕組み構築が図れた。また、社員のモチベーションが大きくアップしたことが一番の財産である。トップ・ミドル・ボトムと全社一丸の活動で収益改革の進むべき道を明確化したことは非常に大きな成果と考える。
2つの事例が示すように、設計が変われば会社全体により良い変化をもたらすことが出来る。品質の良い会社ではコストダウンが進み、大幅なリードタイムの短縮が可能となる。企業価値最大化に向けて設計部門を基軸とした抜本的な改革が今求められている。