本ページでは、株式会社 水田製作所様に対するコンサルティング実績をご紹介しています。
(※ASAP 2018年 No.2より抜粋)
はじめに
株式会社水田製作所は、電気・電子機器向けの樹脂成形品、端子台及びプリント配線基板の設計・製作をコア技術に、成形2次加工並びにユニット設計~製造組立までを行う、受託設計・生産専門の「総合アセンブリーメーカー」である。主に発送電、受配電システムや社会インフラ、FA分野向けの各種部品を中心に、大手電機メーカーのサプライヤーとしてビジネス展開を進めている。
創業は1934年(昭和9年)、83年を越える伝統と歴史を通じて、製品開発~生産の受託によって顧客からの信頼を築き上げてこられた。
同社の特色は、いわば小規模の異なる事業体が複数集まったイメージ。それぞれの部門が自主独立しながら有機的に連携して事業展開を図る点にある。
創業より、電気・構造の技術部門を持ち、部品の製造技術や設備等を保有しながら、総合的なものづくりを進めている。
今回、2017年末に開催されたチャレンジ活動の「第三期 まとめ成果発表会」に同席させていただいた。その発表会からも、各部門がそれぞれの強みを活かしながら、自主独立の精神を持って活動する姿勢がうかがえた。他部門や社外パートナーと連携しながらものづくりを進めるなかで、「自部門と会社の成長を考えていく」その思いが強く感じられる発表会であった。
成果発表レポートとして、「第三期 まとめ発表会」の内容を中心に全員参画で相乗効果を発揮する改善活動の全容を紹介したい。
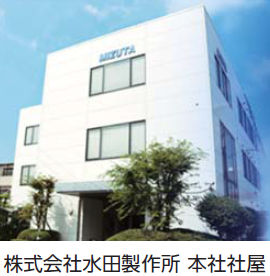
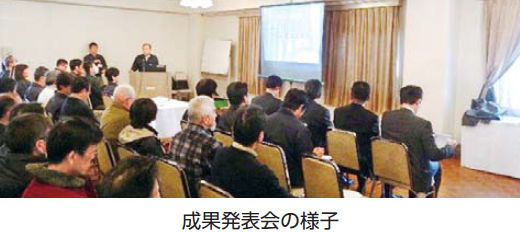
チャレンジ活動の要旨
株式会社水田製作所では、 2015年5月からチャレンジ活動を開始、今回で三期目の成果発表会を迎えた。当初は直接部門の「職場チーム活動」から、その後「上流での品質つくり込み」「コストマネジメント」といった全社横串テーマ活動に発展、さらに三期目からは間接部門の職場チーム活動も加わり、真の意味で“全員参画”の改善活動となってきている。
今日においては、経営トップ層からの「チャレンジ活動方針の発信(トップダウン)」と自主的な「職場チーム活動の推進(ボトムアップ)」を融合させる当初目指していた姿にも近づいてきている。
また、特に目立つのが女性リーダーの活躍である。独創的な着眼点や繊細な感性が活動の牽引力になっていると言っても過言ではない。
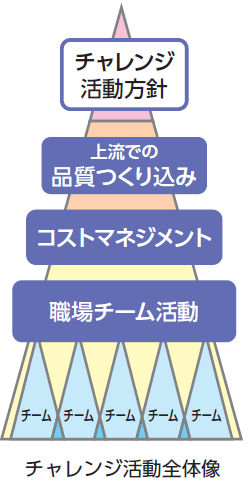
成果発表レポート(第三期 まとめ成果発表会より)
2017年12月29日、1年の仕事納めに合わせて開催された。社員全員が参加するまとめ成果発表会は、全社横串テーマの発表を皮切りに、技術部・品質保証部・管理部や事業開発部などの間接部門、更に、成形加工・基板検査・端子台などの直接部門から熱気ある発表で進められた。
今回は全部門の発表からピックアップした4テーマを紹介する。
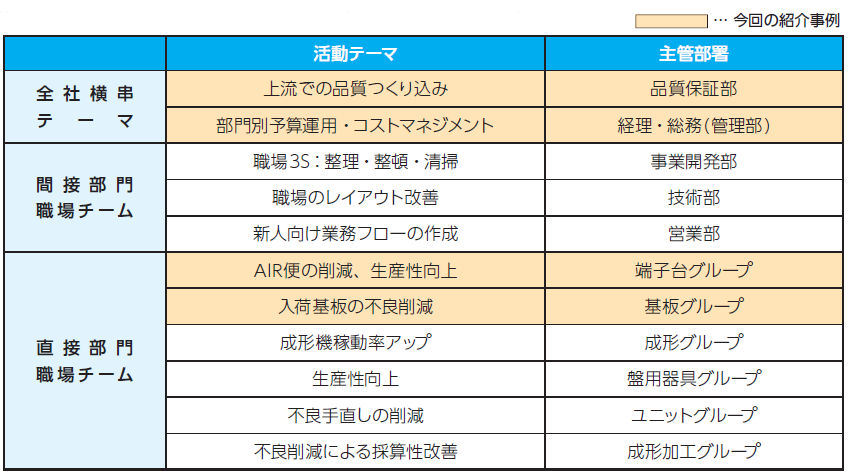
上流での品質つくり込み:品質保証部
品質保証部を主管に、最上流で品質を担保する仕組みに取り組んでいる。従来、全工程のチェックは、最終の出荷検査で実施していた。つまり開発時の問題や金型などの問題も含めた不具合を総合的に検出し、不良流出を未然に防ぐ役割を担っていた。しかし、確認する検査箇所が増加すると、見逃しやヒューマンエラーの発生を誘発する要因にもなる。
また、品質改善の視点からは製造責任の所在が曖昧になることも問題である。たとえば、最終検査でキズが検出されたとしても、それがシルク印刷によるものか、それとも組立で付いたものなのかが品質保証部では判断できない。特に社外パートナーにより発生した品質不良ロスを把握できなければ、社内が負担する不良処理コストも正しく確認できない。そこで、従来の業務フローを見直し、品質が担保でき、きちんとフォローできる仕組みづくりに取り組んだ。
⑴ 業務プロセスの改善
上流での品質を担保するには、現状の業務フローを見直し、目指すべき姿を検討することが必要である。ただ単なる文字の羅列ではなく、いつ・どこで・だれが・何をするか、というチェック項目を明確化する業務フローの再構築に取り組んだ。
ただ、今期の活動では、ありたい姿の描写に留まっており、まだまだ現実とのギャップは大きい。この隔たりを埋める作業がこれからの活動課題となっている。
⑵ 業務フローにおける「ホールドポイント」の設定
業務フローには、責任の所在を明確にするための各ホールドポイントを設定した。たとえば、開発時には3つのホールドポイントを設定し、開発の進捗チェックと責任・承認の所在を明らかにする。また、量産時には、受入検査、中間検査、出荷検査の実施を明確にする。これにより品質保証部が本来の出荷許可を行えるようにしていく。
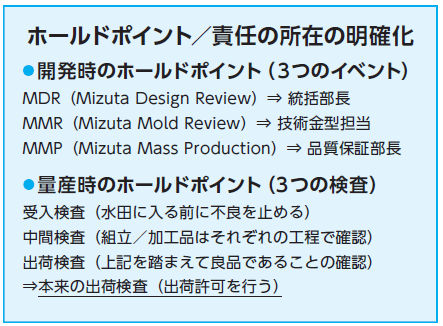
⑶ 再発不良を防止する「顧客要求事項確認書」の作成
再発不良を防ぐ手立てとして、顧客からの要求を明確にする「顧客要求事項確認書」を作成した。これは顧客の要求事項ならびに顧客から寄せられた過去の不具合をチェックするものである。量産前に上流でチェックすべき項目を部門間で情報共有し、確認漏れを無くすことで再発不良を未然に防いでいきたい。
⑷ フォローアップの仕組みづくり
ルールを作っても社内に浸透しない、守られない、途中で消えてしまうといったことが過去の活動では多かった。そこで業務フローの遵守をフォローする仕組みとして、「金型関連定例会議」を2016年12月から約1年にわたり毎週実施してきた。
会議の中では、「金型進捗管理表」を使い新規金型受注に関する情報共有化と同時に、業務フローの問題点の抽出を行ってきた。今後は状況の連絡や進捗管理に留まらず、業務フローの見直しから問題点の解決などを検討できるようにしていく。
今回の活動では、あるべき業務プロセス、ルールや帳票類の作成を実施した。今後は事例を積み重ねながら問題や修正点を共有化し、都度改善を続けることで、チェック体制の精度を高めていく。
これを完成して確実に運用できるようになれば、最終検査が全責任を負うという問題が解決され、品質トラブルをゼロに近づけることで損失も減り、会社の信頼性も向上する。このようにすることで自ずと儲かる仕組みにしていきたい。
部門別予算運用・コストマネジメント:経理・総務(管理部)
管理部では、各部門の予算運用を把握し、その損益構造を明らかにするコストマネジメントを進めている。その目的は、各部門に与えられた経費予算と実績を集計し、全体の経年比較で損益構造を検証、全社的な収益性の改善に繋げることである。各部門に付与された月別予算を可視化し、各経費の発生状況や部門間の偏り、使いすぎなどを改める狙いを持っている。
物品金額の予算については資材部で管理しているが、全体の経費を一覧化(月別)することで、経費の発生を可視化し、使いすぎの抑制を図った。また、前年比の分析も実施し、各部門に対するコストの監視~提言を、管理部から発信することにした。
予算が与えられるから使うのではなく、使うべきところに予算を投入する。そして、安くて良いものを最適な条件で購入し、業務改善に役立てる。予算活用の費用対効果を高めることが改善の到達点である。この取組みを通じ、各部門においてコスト意識が着実に高まってきたと感じている。たとえば、新たな物品を購入した場合の改善効果がしっかり評価されるようになった。今後は更に、各部門の予算策定を精度よくできるよう、管理部がリードしていきたい。
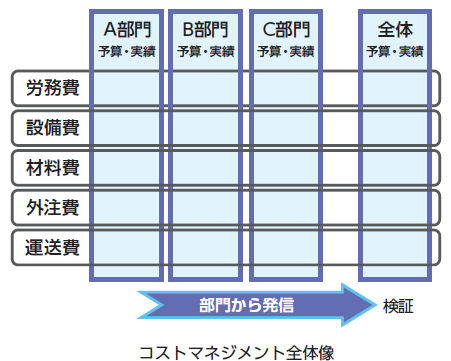
AIR便の削減、生産性向上:端子台グループ
端子台グループでは、AIR便の削減、生産性向上の2つを軸に活動を進めてきた。
⑴AIR便の削減
海外のパートナーであるO社では、納期関係でAIR便を使用する場合がある。その費用は当社が負担してきており、今回はその削減に取り組んだ。まず、対策として、納期フォローの回数を1回から2回以上に増やした。次にO 社側に交渉して、リードタイム通りに発注したものについては、O社にAIR便の経費負担をしてもらえることになった(2017年4月後半より)。
また、顧客からの長期計画に過去6ヵ月の平均値を加味して、安全在庫の基準を変更し、それに基づいて納期設定の改善を行った結果、AIR便は8割近く削減した。
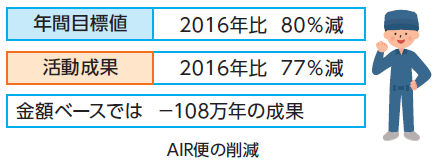
⑵生産性向上
チャレンジ目標として、1時間あたりの生産性110%を掲げた。
改善として、新人とベテランの作業をビデオ撮影、両者を比較して作業のムダの洗い出しや効率の良い方法を検討、意見をまとめ、具体的な改善策に向けた試行錯誤を積み重ねた。
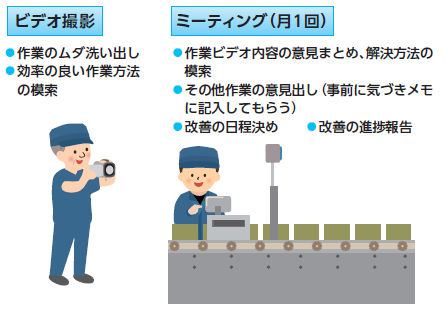
⑶具体事例の紹介
1.端子圧入治具の見直し
改善前はバネで開閉する冶具に、製品を圧入して固定を行っていたが、治具に製品をセットするのに時間がかかり、バネが硬くて手が疲れるため、長時間作業できないという現場の声があった。そこで新たな治具の制作を考えたが、検討の中で、そもそも製品を固定する意味がないことがわかり、バネを省き置くだけの簡単な作業とした。これにより1個当たり10秒の時間が短縮され、作業者の負担が軽減した。
2.端子台の工程改善による原価低減
改善前はO社で組立・外観検査・梱包・出荷までを行っていた。当社では、受入後に外観検査・トレイに梱包して出荷となる。ここで疑問に思ったのが、同じ検査が2回も実施されていることである。そこで、O社に画像検査機導入による外観検査ミス防止を図らせるとともに、ピン検査の作業指導を行った。
これらを通じて当社での外観検査を抜き取り検査に、ピン検査を廃止した。梱包についてはO社がトレイで出荷しない理由について検討し、改善を要請し、トレイに入れて出荷してもらうようにした。
これにより当社で重量を計ってトレイに入れ替える必要がなくなった。 また、数量管理については、箱単位の重量データをパソコンに送信して自動判定し、記録できるようにした。
これらの改善により年間で140万円の削減に繋がった。
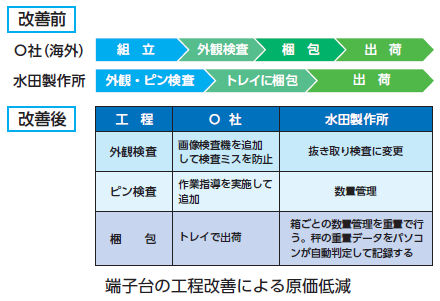
入荷基板の不良削減:基板グループ
基板グループでは、社外パートナーからの納入品における不良率低減という難しいテーマにチャレンジし、不良率を着実に低下させる結果を出した。
社外パートナーに対する①品質改善パトロールの継続、②品質要望書の提示、③品質指導の継続などを通じ、社外パートナーに積極的に介入することで品質問題を解決していった。
⑴ 社外パートナーM社の事例
不具合検出率を上げるために、M社について検査エリアのレイアウト変更を指導した。以前は検査机が照明に対して交差するように配置されていたが、これでは照度不足による見落としの可能性がある。そこで、照明に対して平行になるように検査机を配置した。これにより、検出率をアップし精度向上につなげられるのではないかと期待している。
今までの指導では工程内の改善を進めてきたが、今後は検査工程での改善を継続していきたいと考えている。
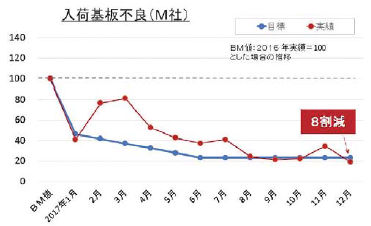
⑵ 社外パートナーT社の事例
T社の改善では、異物不良の削減に取り組んだ。これまでも検査工程での検出率を上げるための削減活動を行ってきたが、それだけでは限界がある。異物の種類を特定する分析では、過去に中断した経緯もある中、今回再調査を依頼し、異物の特定と今後の対応策などを行う「異物付着改善提案書」を提示してもらった。その結果、T社からの不良品は確実に減少傾向にある。
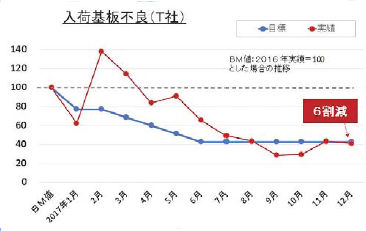
⑶ 海外パートナーR社の事例
海外のパートナーであるR社では機種ごとの不良率に大きな差が見られる。その理由は、他の2社と異なり同機種をまとめて一度に検査するやり方にあると推測した。また、機種検査の順番で不良率が大きく変動する傾向があり、予測が立てにくい。そのためR社については、半年平均での削減を目標とし、改善では圧倒的に多い異物混入の対策に集中した。また、R社内の検査工程においても、AVI検査機の適応範囲を広げ、パラメータの変更を実施し、検出精度の向上を図った。
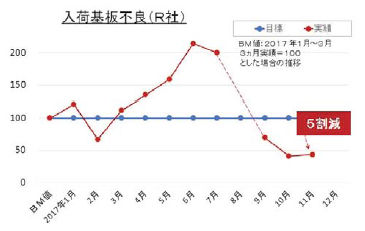
今後の取組み
2018年度の「チャレンジ活動」は四期目に入る。今後に向けた活動方針を紹介したい。
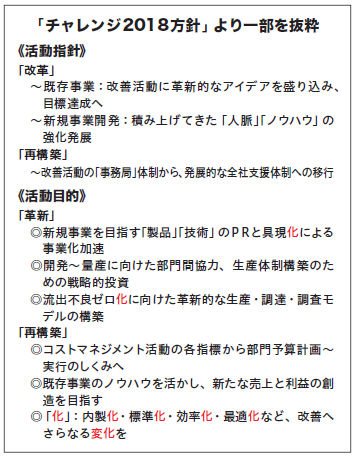
取材後記
まず、発表会に参加させていただいたことに心からお礼を申し上げたい。各部門の発表をお聞きし、全員で改善活動に取り組む姿勢に強く感銘を受けた。
どの発表者の皆さんも、とにかく明るく元気!そして、発表を聞く活動メンバーも真剣そのもの。発表会に参加させていただいた我々も大いに活力を与えられた次第である。
「活動に取り組む熱意・改善成果の創出・トップ自らの評価」が社員にやる気と達成感を与える善い循環となっている。そして、それらが一体となって今後もより改善を進めたいという意識につながっていると思う。今後の更なる飛躍に向けた皆様の取組みにエールを送りたい。
担当コンサルタント