本ページでは、株式会社安川電機様に対するコンサルティング実績をご紹介しています。
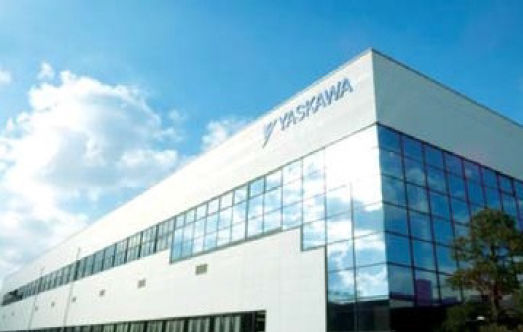
2015年に迎える100周年を記念した安川電機の「ロボット村」構想。北九州市が推進する地域開発プロジェク トとも連携して八幡西事業所の広大な土地に建設が進められている。
この「ロボット村」には一般の方が自由に入れる 「YASKAWAの森」を設けるなど、ロボットを中心とした安川電機の事業を楽しく体感・体験できる空間を提供。 人とロボットが共存する新しい社会を創造するための情報発信を行い、北九州を始めとした地域の活性化や日本の 「ものづくり」の街・北九州の凄さを世界にアピールする機会に繋げていく。
機械と電気を融合したメカトロニクスの概念を世界に先駆け提唱した安川電機。
永い歴史と伝統で培われた技術力を基盤に、グリーンエネルギーの高効率活用や、人とロボットが共存する社会 の実現など、新たな事業領域である“環境・エネルギー”“ロボティクスヒューマンアシスト”分野に対する取り組みを本格化している。生産体制では国内のものづくり機能を新工場群に集約一本化、中国工場との二極体制で世界の 市場をターゲットとして未来に向けた拡大戦略を続けている。
今回のテーマは、その新工場建設に合わせた半導体用ロボット部門の生産革新。工場・製品・人を変える「最適なものづくり」のための全員参加の活動をレポートする。
(※ASAP 2014年 No.1より抜粋)
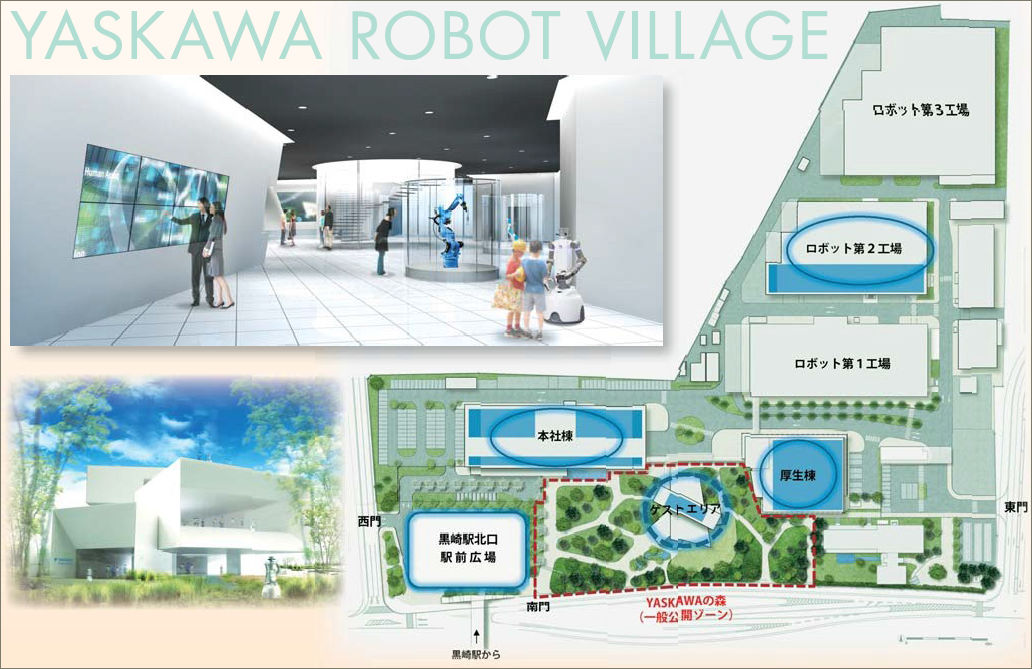
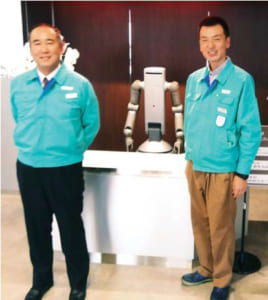
左:株式会社安川電機 生産・業務本部
先端生産技術センタ長 藤原 博昭 氏
右:安川マニュファクチャリング株式会社
ロボットカンパニー第2生産部 第2製造課 課長 末光 真一氏
生産革新活動の概要
本日はよろしくお願いします。最初に今回の生産革新を始められた背景をお聞かせください。
藤原:
当社では以前より各工場単位で生産革新活動を展開してきました。ところがリーマンショックの影響 で生産量が一気に激減し、それまで実施してきた革新活動が一時停滞する状況に陥りました。
リーマンショックが明けた後も、部門別の改善活動は続けていたのですが、工場全体レベルでの改善活動は途絶えて久しい状態で、革新活動の経験者や、革新に 積極的な人材も減少したなという感覚が強くなりました。
その後、安川電機として全社的な生産革新を求める機運が高まり、活動再開に向けた検討を始めることにしました。
活動の再開にあたってお考えになったことは何でしょうか。
藤原:
今回は受注系、調達系、生産系といった全体の流れを通した生産革新活動を工場レベルで再開したいと考えました。また合わせて、その活動成果を他部門や他工場にも横展開するというストーリーで進めることにしました。
そのため、どの工場をターゲットにして実施するか検討するため、各工場に対しヒアリングを行ったのですが、ちょうどそのとき、100周年事業のミッションと して半導体ロボット部門に与えられた課題が浮かび上がりました。それは、これまで3ヶ所に分散していた生産機能を、この八幡西事業所内に集約し、新たな生 産拠点(工場)を建設するというものでした。
そこで、半導体ロボット部門を生産革新活動のモデル工場としてスタートさせることにしたわけです。
コンサルタント活用は初めてとお聞きしましたが。
末光: 従来、当社の活動は自主改善が中心で、社内人材のパワーを有効に活用して進めてきました。初めて の外部コンサルタント導入に踏み切った理由は、活動の停滞を防止し、改善・改革のスピード感を高めるためでした。
藤原: コンサルティングの検討にあたっては、できるだけ幅広いコンサルタントの意見をお聞きしたいと思 い、複数社にお声がけをさせていただきました。各社に1日診断およびプレゼンテーションをお願いしたわけですが、その中で当社が考えている内容に一番近い 提案をいただいたのがテクノ経営でした。当社では、特に革新人材の育成も課題となっていましたので、テクノ経営が提示する「人を基軸にする革新」というコン セプトが合致したわけです。
今回の活動課題についてお伺いします。
末光:
半導体用ロボット部門の活動開始は2011年10月からですが、それまでは個別にお客様の要求に よりカストマイズされたロボットの生産が中心でした。各機種により異なる一品一様の製品づくりが主流のため、ライン化することは容易ではなかったのです。
ところが2011年に入ると半導体用ロボットにも標準化の動きが現れてきました。当社の製品でいえば、SEMISTARという標準ロボットとしてライン生産が できるようになってきたのです。そこでラインとしての革新を起こして生産力を伸ばして行くという新たな可能性が生まれてきました。活動対象は半導体用ロボ ット製造の生産ラインで約80名の人員が対象です。活動は、2011年11月~2013年10月の24か月で進めることになりました。
活動開始前の稼働状況の観察では、全体的に作業者の動きにスピード感がなく、時間の意識が希薄であるという結果でした。
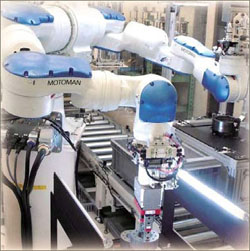
工場や製品の“つくり”を変えていく と共に、作業者の意識改革が求められていました。活動は新工場での生産に向けて、①最適レイアウト構築、②工数削減、③意識改革を中心としました。 また創業100周年に合わせた新工場建設で、私たちの半導体用ロボット生産ラインの集約も決定したわけですが、その期限に合わせた新工場のレイアウトや動線 改善にも取り組むことにしました。
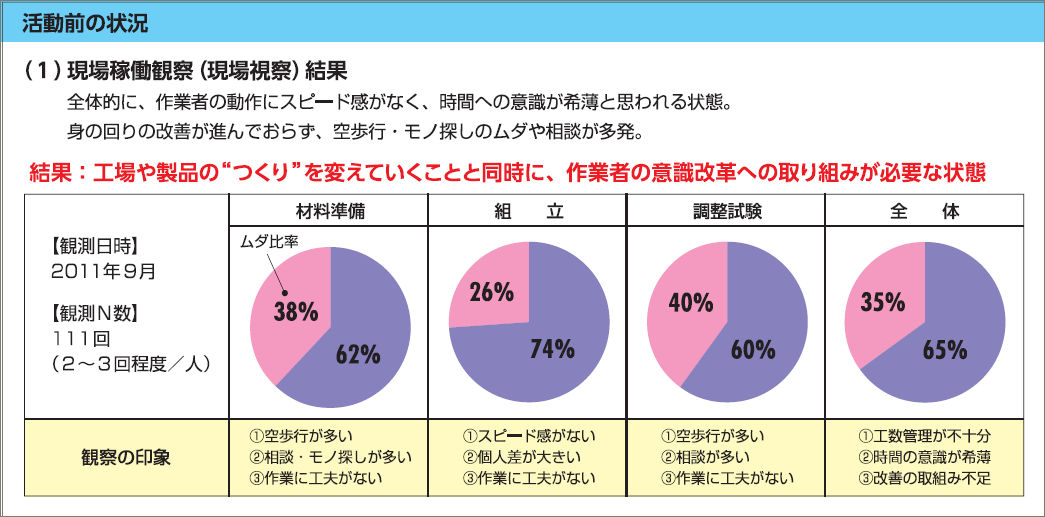
活動方針や活動目標等はどのように定められましたか。
末光: 活動方針は『最適なつくり』による未来の獲得”とし、活動名称を“CHANGE3”としました。これは 工場・製品・人の3つを変えて最適な“つくり”へチェンジするという意味です。工場は「最適動線と柔軟さを兼ね備え、徹底的にムダが排除された、魅せるに 値する合理化ライン」に、製品は「知恵と工夫が反映され、生産性が高く、ミスをさせない理想的な製品」に、人は「作業者自身が問題に気づき、自ら改善を行う、 モノづくりのプロ」に変わることを目指しました。活動の定量目標は、生産性150%達成、定性目標は気づき活動の推進による作業者自身のレベルアップとしま した。
生産革新活動の実際
工場における動線分析とレイアウト決定の活動についてお話ください。
末光:
工場革新のねらいは、部品入荷から製品出荷までの一貫した「最適動線」を確立することと、多品種変 量に即応できる「柔軟なラインと組織」を構築することでした。
改善のステップを繰り返しながら最終的なレイアウトを決定させました。①~④の改善ステップでは現状分析と問題抽出を実施。既存のレイアウトから抽出され た問題点を確認・整理して9項目の基本要件(作業性、安全性、品質、拡張性、融通性、快適性、スペース有効性、管理の容易さ、外観宣伝効果)を検討していき ました。
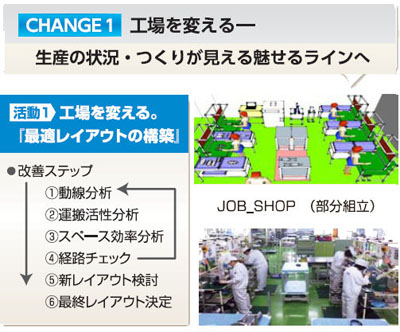
新工場建設のタイムリミットがある中、どんな点に苦労しましたか?
中川: 手法的には「こういう手法です」という風に演習問題を通じて習得して頂きました。そして実際にレイ アウトを考える際に必要な計測・調査を行って、基本要件を満たすまで、それを何回も繰り返すことによって、どんどんレイアウト構想が醸成されていきました。 その過程では担当された皆さんは結構大変だったのではないかと思います。100回位レイアウトを書き直したと冗談まじりに言われてましたので。
末光:
そうですね。結構彼らも頑張ってやりました。3Dとかを使ってレイアウトして、本当に現実に近い ものを作って。スペースも30%削減を目標にやっていました。
今振り返ると、工場のレイアウトのアイデアというものはどんどん変わっていくものです。それに合わせて基本的な計画や考え方も変わる。変更があれば新たな PDCAを回してまた同じロジックで考えていく。その中でその使い方とか考え方が習得できたので逆に良かったかもしれません。最終的には最適動線により移 動距離が1/3に短縮できたので苦労した成果があったと思います。
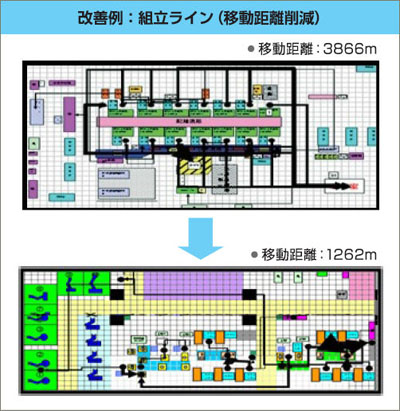
現場にスピード感を与えた作業改善についてお話ください。
末光: 改善ステップとしては、すべての作業工程をビデオ撮影し、ひとつひとつの作業・動きを分析して問 題点を抽出しました。個々の作業については、E(排除)、C(統合)、R(代替)、S(簡素)の視点で改善具体策を立案し実行しました。また工数管理の メッシュを15分単位として、各作業者が自分自身で進捗管理できる仕組みを構築しました。
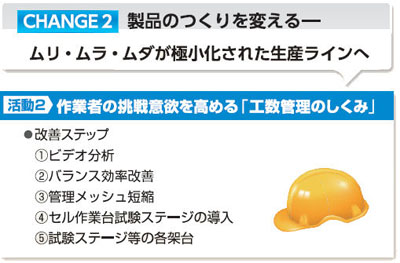

セル作業における改善事例についてお伺いします。
末光: セル作業の改善はMTM(メソッド・タイム設定法)により動作時間を算出して比較評価。各工程に おいて治工具が最適配置されたセル作業台を自分たちで設計しました。その結果、移動距離が短縮され、不必要な動作やムリな動作がなくなりました。
中川: セル作業台を導入するにあたっては、どんなにスタッフが理想的だという案を考えても完成度は七割位しかない。作業者の方がそれをベースに「あれやこれや」と好きにアレンジして完成度を高めていくということが重要です。実際にいろいろ工夫して「これは ここに置いた方がよい」という風に皆さんが自ら改善して使いやすいベストなセル作業台が完成しましたね。
人材育成に関する活動の取り組みにおける重点ポイントは。
末光: ラインを変えるためには、その前にまず人材をつくることが重要。当社では作業者にスピード感がな いという課題もあり、当たり前でやっている作業だが「本当にそれでいいのか」というところに気づいてもらえる活動。そういう人材を育てたいという思いがあり ました。具体的には、作業者のマインド部分を強化する“気づき活動”と生産技術に関する“ものづくり勉強会”を開催しました。この勉強会は活動の2年間で改 善技術者を養成することを目的に、基本的な生産レベルの知識を習得するものでした。
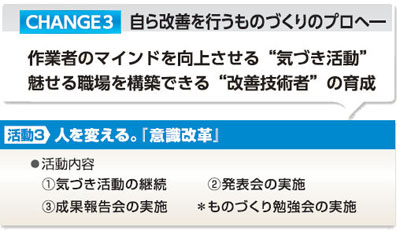
“気づき活動”は参加者にたいへん好評だったとお聞きしていますが。
末光:
コンサルタントの中川さんからの提案もあり、気づき活動を導入することにしたのですが、確かに非 常に効果的な活動であったと思います。“気づき活動”は何でも気づいたことをメモの形で提案するものですが、いきなり対策を求めるのではなく、先ず身の周り の問題に気づくことによりセンシティブな発見力を高めることを目的としています。気づき活動は「問題だけを出す」そしてその「対策はみんなで考える」という、 そこを切り分けて実施してきたことが一番浸透しやすかったポイントだったと思います。
“気づき活動”は毎週行って、成果発表会を月1回実施していきました。発表会では全体に各チームが自分たちの活動内容をお披露目して、相互に意見交換ができ る場としました。発表された活動には「こうしたほうがいいのではないか」と参加メンバーがコメントを述べ、「自分たちもどんどん展開しよう」という風にどんどんマネを始める流れが生まれてきました。
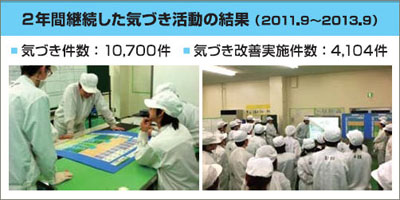
藤原: 人間というものは思いついてもすぐに忘れるものなので、すぐにメモを取ることが大切。何でも「気 づいたこと」「考えたこと」「こうしたいと思ったこと」はすぐメモする習慣を身に着けたいものです。後でやろうと思っても、そのうちに忘れてしまうことが多い のです。思いついたことをすぐメモする躾といいますか、仕組みづくりが大切です。今まで思っていたが表に出なかったアイデアが集まる“気づき活動”は誰も想定 もしなかった効果が出てくる可能性もある活動だと思います。そのあたりは私も見ていて評価すべきところだと感じています。
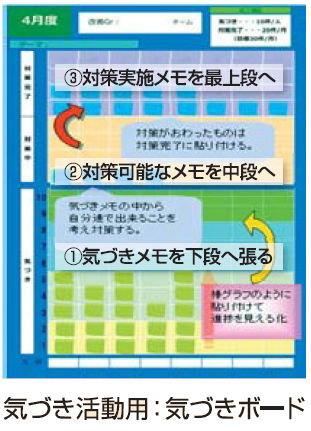
九州地区のQCサークル活動でダブル受賞
QCサークル活動のKAIZEN発表大会で優勝されたとのことですが。
末光:
今回の“気づき活動”は、九州地区の改善活動発表大会(第5532回 QCサークル北部九州大会 ・2013年10月11日)において「地区長賞」と「福岡県知事賞」をダブル受賞しました。
九州地区でも、相当な改善が進んでいる自動車産業等の企業に打ち勝ったことは驚きです。そして、これを機に気づき活動に対する社内の関心が一気に高まりました。今後は推進部門が主体となって全工場に積極的に“気づき活動”を広めていきたく考えています。
気づき活動が高い成果を出した理由はなんでしょうか。
藤原:
気づき活動を成功させる秘訣は毎週継続することです。ノルマを決めて毎週、毎月で完結させるとい うことが重要です。PDCAをちゃんと有効に回す取り組みを継続的に実施していく。その仕組みを作り上げることが一番重要ではないかと思います。
更に1年、2年、3年と積み重ねることで提案するレベルも上がっていくし、メンバーの意識の思考もピュアに鋭くなってくるものです。
今後に関して“気づき活動”を全社展開されていくのでしょうか。
藤原: 気づきメモの件数は、2年間で1人100件近く、全体では10,700件に達しました。活動前は1人平均 で出ても数件というレベルでしたから、何十倍という成果です。それだけいい仕組みが定着したのではないかなと思います。今までも各工場の取り組みを他の工 場に波及させる試みがありましたが、実際にはあまり広まっていないのが現状であったと思います。それを今回は“気づき活動”に特化して全社展開につなげていきたいと考えています。
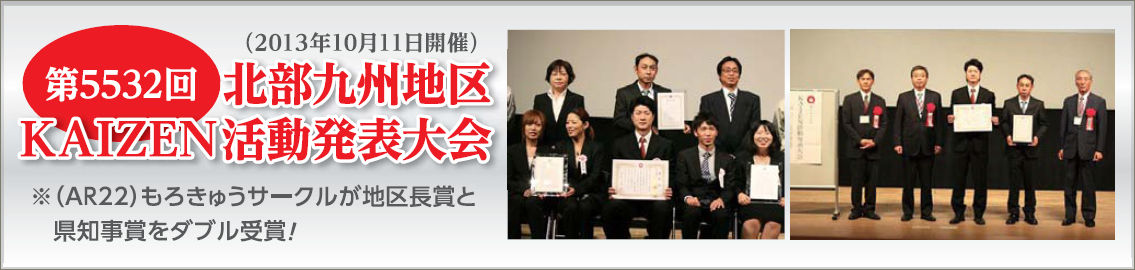
生産革新改善での苦労話
改善活動の苦労話がありましたらお聞かせください。
末光:
週1回の活動では、改善リーダーと事務局の私と現場の担当者が参加して改善をしてきました。その とき対策等はもちろん考えているのですが、やるべきことを決めてその1週間後までにやってくる。これには改善リーダーや私も含めてたいへん苦労しました。
1週間が経つのは速く、またすぐに次の活動日がやってくる。そういう意見が最初のうちは出てきました。しかし、活動を継続して実際にどんどん成果が出てくることで、やり方も含めて効率よく進めることができるようになると毎週木曜の活動日も苦ではなくなってきました。
確かに1週間というサイクルは短い感じもしますが。
末光: 毎週木曜が指導日としますと、各現場で確認して月曜日には現場に伝えて、火曜日には事前の打ち合わ せをしてという感じでほとんど休む暇がありませんね。
藤原: 1週間という期間は実は非常に絶妙なサイクルだと思います。例えば、1か月という期間があったと しても、結局頑張るのは最後の1週間位ではないでしょうか。ところが1週間しかなければ休めるのは月曜日だけ。火曜日から金曜日は一生懸命頑張らなくてな りません。今回の活動では、1週間という活動のサイクルでPDCAを回すことが習慣化できて改善が一気に進みました。
活動事務局としてご苦労された点は。
藤原:
ちょうど1年位たったときのことです。それまで順調に伸びていた生産量が急に低下する時期がありました。するとそれと同時に活動の生産性指標も伸びなくなった。そこをどうリカバリーするか、原因は何か、どうすればよいか。私どもと末光でかなり頻繁に やり取りして、どう数値(生産性)を維持するか、その対策を色々と協議し、実行したことが非常に苦労したところです。しかし、2年間の中でそういう機会に 遭遇したことは逆に良かったと思っています。それにより取り組むべき課題が見えてきましたから。
同じ活動をしていても生産性が落ちるときがある。そのときは落ちる原因は何かを探る。現場ウォッチングすることで原因を観る。そういう時期があって良かっ たと思います。なぜ生産性が落ちたのかが明確になっていれば、次に同じような状況に遭遇したときに「こうすればよい」ということがわかります。必要最小限 のリカバリーをするにはどうすればよいか。そんな知識が身についてきたのではないかと思います。
末光: そこが本当に苦しかったです(笑)。2年間で2回ほどそういうことがありましたから。そのときの教訓を生かして生産性が落ちないようにしてきました。
藤原:
それが今後の活動のひとつのキーになると思います。半導体事業というのは負荷変動が非常に大きい 特色を持っています。半導体サイクルによって多い時期と少ない時期の差が激しい。そうした中で生産性を低下させずにいかにリカバリーするかという方策がこ れからのためにも重要になってくるのです。
そういうことがこうしたタイミングで考えることができました。当時は相当苦労しましたが今となっては良い経験でした。
おそらく順風満帆に行っていたら、そういうリスクを感じることがなかったでしょう。どんな活動をやっていても必ずリスクが存在する。リスクの原因は何で、 どうリカバリーしなければならないかがある程度見えてきたことが良かったと思います。
生産革新活動の成果
今回の活動成果についてお伺いします。
末光:
活動成果としては3つあります。まず、工場の最適レイアウトでは、生産性の高い最適な動線を構築 できたことです。次に工数削減という面では、7種類の主要機種に対する改善で、ビデオ分析によるムダ取りで工数削減が実施できたことで、この活動でも7機 種中5機種が目標の生産性150%をクリアしました。
また、気づき活動による意識改革ということでは、今までお話したように人材育成やスキルアップにつながる成果が出ています。自分たちで気づいて改善を行う という自主性を養うことができたと思います。
今後の活動に向けたお考えやビジョン等をお聞かせください。
藤原: 最初にお話した「ロボット村」構想は、創立100周年を記念して地域貢献につながるプロジェクトとし て計画されたものです。市民に開放したスペースとして「YASKAWAの森」を設け、入館自由でロボットに関する展示や体験ができる「未来館」を2015年3月完 成に向けて建設中です。同時に現在建設中の本社および新工場も、分散していたロボット事業を集約して世界のマザー工場とするものです。会社ビジョンとしては、 少子高齢化に対して当社のコア技術を活かしてどう解決していくか。そのために、より人に近い領域でロボットを活用するための“ロボティクスヒューマンアシスト 事業”と環境問題ではインバータ電力変換の技術を使った“環境・エネルギー事業”。この2つを事業の柱として取り組んでいきたく思います。
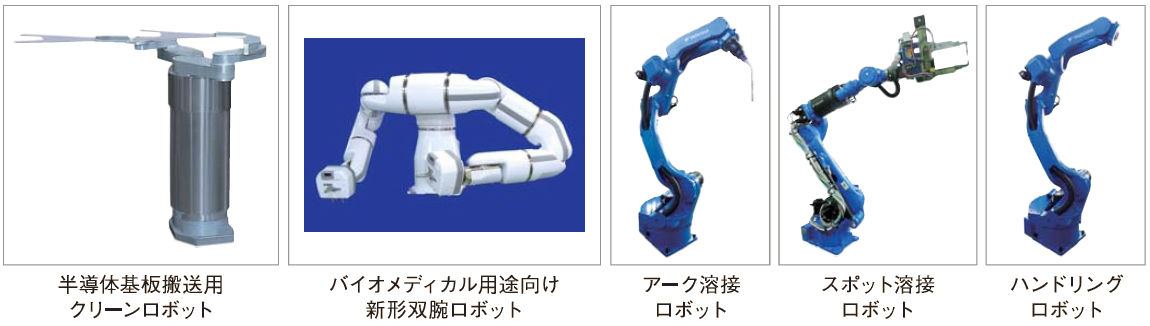
末光: 今後の活動については、各組立工程での生産性向上ができましたので、これからは全体のリードタイ ムや流れの停滞をなくすという課題に取り組んでいきたいと思います。また、今後は新機種も出てきますので開発時点から量産ラインに流すことを考えながら、最短 で品質的に満足のいく製品が作れるように改善の成果を反映させていきたい。また今回学んできた改善活動を他職場に水平展開して、さらにロボット工場全体につながる改善活動に発展させていこうと考えています。
中川: 気づき活動では、作業者が自らの作業を振り返って、改善することで改善マインドを高めていく。ス タッフは、更なる効率UPの構想案を作業者に提示し、試行する。そして、この試行による問題点を気づき活動で改善していく。この作業者とスタッフの役割がうまく機能したと感じます。
藤原: 現場主導の改善といいますが、職場が一体となり全員参加で進めることが大切です。ある特定の人の力によるのではなくて、全員で作り上げるという感覚が重要だと思います。終わりなき改善に向けて全員が一体感を持ってやり遂げれば満足できる成果は必ず実 現できるはずです。そういう意味で今回の活動は組織としての満足度が非常に高い結果になりました。