2014.07.12
国内製造業で勝ち残る ローコスト・高品質生産体質への改革
- 関連タグ:
-
- 現場改革・生産性向上
- 人材育成
- 間接部門改革
- 技能伝承
- 部門間連携
- 品質改善
- 設計部門改革
執筆者:

大野 浩行
全社改革は“活人化プロジェクト”で進める
ある専務さんからのご相談
数年前、ある電子部材メーカー(A社)の専務さんとお話する機会がありました。
中国や韓国そしてアメリカなどに生産拠点を移し、国内はお客様の要求水準が高い製品を造るマザー工場だけになっている。そして海外生産では利益が上がっているが、多品種少量生産が主流の国内工場では利益が圧迫されている。社内で推進する改善活動も期待する成果が出ず、抜本的な打開策を模索されているとのことでした。
それがきっかけで工場診断をさせていただき、もう3年以上になりますが、現在もコンサルタントとしてお付き合いさせていただいております。
国内生産で勝ち抜くための鍵は品質とローコスト生産体質の追究にあります。今回はA社の事例を中心に生産体質を改革する“活人化プロジェクト”についてお話いたします。
行き詰まる改善活動
A社は日本でもトップクラスの製品開発力を誇る企業です。ところが工場を拝見した結果、コスト的な対策が不十分であることがわかりました。国内では関東にマザー工場を設置され、開発から生産、営業までの一貫体制を築かれていますが、多品種少量で品質・コスト水準の厳しい国内生産では利益の出にくい構造になっていたのです。顧客である機械、自動車メーカーからの厳しい品質・コスト・納期等の要請。そして、高い精度が要求される条件下、クレームの発生もしばしばです。全社的なムダ・ロス削減によりコストと品質を両立させていかなければ非常に厳しい状況になっていました。専務や社長はこの非常事態をいかに乗り切っていくか。それに頭を悩まされているのですが、内部で改革をしようにも活動が行き詰っている。現状を打破するシナリオがないというお話でした。
「そうか、なるほど」キーワードは活人化
A社からは3年計画での現場改革のプランを求められました。そこで私が提案させていただいたのが“活人化プロジェクト”による3年計画の処方箋です。ちなみに活人化とは、現場改善(少人化)により生まれた余力を全社的な改革に振り向けることです。各部門の精鋭を結集してプロジェクトを編成することで高い成果が期待できます(図1)。
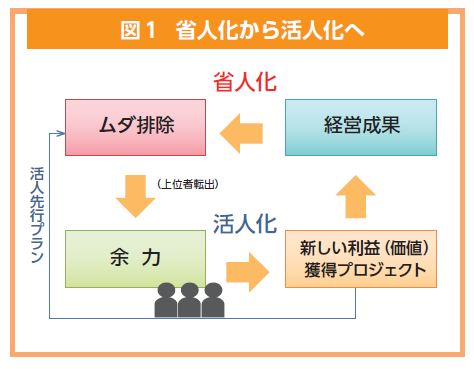
メンバーに対する動機付けがないと活動は上手く行きません。また中長期的なビジョンを描いて進めることも大切です。ビジョンの共有化はメンバーに夢を与えます。そして、その目標に向かって推進体制を組織し活動がスタートします。
リーダーの責任と権限、各メンバーの役割を明確化することも成功の条件です。また活動の達成度合いを把握・評価できる生産性の指標の存在も重要です。間接部門ならばジョブリスト、生産現場なら不良率低減などの数値目標も指標づくりの資料となるでしょう。生産性指標の共有化により、努力の有効性が認識され、活動に対する使命感や一体感が組織に生まれてきます。プランの1年目は、間接・直接部門の改善からスタートです。まず現場の現状分析、それを明確にするためには業務構造を露わにすることが必要です。どのくらいの工数がかかっているか。どこに問題があるのか。その落とし込みを行って、構造の分析と数値化により問題抽出をはかります。
A社では、まず間接・直接部門を対象にムダ業務の削減を行うと共に技術技能伝承の仕組みをつくって、全体的な生産性のレベルアップを進めました。
2年目からは“活人化プロジェクト”により全体改革を具現化する準備を進めていく。これを活人化の先行管理と呼んでいます。
そして3年目にかけて“活人化プロジェクト”で3つの競争力を付ける。
その3つの競争力とは、1)コスト競争力、2)品質力の強化、3)新製品の提案力です。具体的には以下のようなテーマとなります。
1 コスト競争力プロジェクト
圧迫する外注・加工費の低減。現状人員による内製化を推進。自社ならではの生産技術を構築。
2 品質競争力プロジェクト
品質不良を1/10にするため設計起因の品質不具合をなくす。生産部門では製造ミスの撲滅、判断力ミスによるロス防止。
3 新規提案力プロジェクト
新規開発製品の提案プロジェクトを発足。技術イノベーションのツール化。各部門の精鋭を結集した戦略的CSチームを編成。
これらの競争力は相互に密接に結びついており、いずれも国内マザー工場として備えるべき能力です。そして、全社を横断的に捉えるプロジェクト改革であってこそ達成できる大きなテーマでもあります。
改善活動によるムダ削減や省力が進むと、現場業務が少人化されてきます。つまり工数削減によるコストダウン効果が出てくるわけですが、せっかくの活動も単なるコスト追求だけではジリ貧になってしまいます。部門改善を全社改革に結びつける“活人化プロジェクト”こそ、現状の行き詰まりを打破する方策です。
「活人という考え方があったのか」――そのことを専務さんにはご理解いただくことができました。
“活人化プロジェクト”は間接・直接部門の改革から
間接部門の改革
“活人化プロジェクト”を実現するには、まず間接・直接部門を徹底改善して余力創出をはかることが必要です。ここでは誌面の都合で、間接部門を中心にしたポイントを取り上げてご説明します。
まず間接部門の業務は見えにくいという特質があります。そこでまず業務を分解していくことで見える化をはかる必要があります。部門リーダーを中心に自部門の業務を書きだしてみます。例えば、品質保証にはどんな業務があるでしょうか。クレーム対応、原因分析、原材料確認…。これを大区分、中区分、小区分と区分けして一覧表にしてみます(図2)。
これにより各業務における工数の比重や担当者が一目でわかるようになります。例えば、品質保証の業務で「お客様のクレーム対応」が非常に多いとすれば、源流管理が本来の業務なのに事後対策に走っている。「これはムダ業務では」ということがわかります。そして、ここから優先順位のウエイトづけにより改善対策を進めていくことができます。また小区分をさらに業務フローのレベルで見ていくとダブリ業務の以外な多さに驚きます。
「昔からやっているから」――過去からの習慣で続けられている曖昧な業務。「何のためにやっているのか」、「止めても特に問題はないのでは」、その曖昧さに気付かせることが大切です。残業が多くなるのは自分たちで業務を作りだしているからではないでしょうか。何かミスが発生すると、その対策で仕事が雪だるま式に増える。しかし、忙しさに振り回されるだけで、なぜ問題が起きるのかが追究されていない。
ポカミスをしない仕組みづくり、必要なときに必要な業務ができているか、必要以上にやっていないか。もっと仕事をシンプルにできないか、目的だけを達成するにはどんな手段があるか、他のアイデアがないか。こうした議論を通じて意識を変えないと人は変わりません。
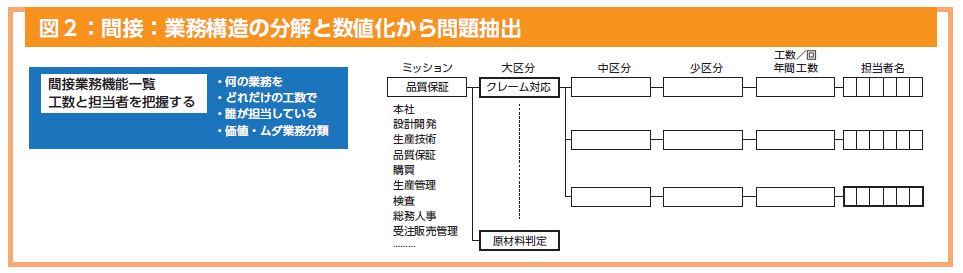
設計部門の活人化
設計者の余力を出すためにどうやって活人化を進めればよいのでしょうか。A社が求める3つの競争力の一つ、新規提案力プロジェクトには優秀な設計者が必要です。
設計ガイドラインは整備されているが、実際には設計プロセスにバラツキがある。昔は相談できる先輩社員がいたが、現在では設計部門の人員も減少し、具体的な設計技術が教育されていないという背景がありました。
これにより手戻りが発生する。この設計で良いだろうと現場に流したが上手く行かない。やり直す事により現場の動きが遅れため残業で対応する。そしてお客様からクレームが出るという具合でFコストがどんどん蓄積されていきます。
技術力がないために納期が遅れるのですが、上司からは結果だけを求められる。しかし、結果をつくるためのプロセスが教育されていないために、製品品質のトラブルやクレームが多発しているわけです。そして、その対応に追われる。これでは高品質・ローコストの生産はなりたちません。
そのために私は設計部門の標準化を提案しました。ただ「こうしなさい」ではなく、なぜ「そうしなければいけない」のか。原理原則で考えるよう習慣づけること。
顧客からの要求条件は数値化をはかり、なぜ必要なのかを明確にする。要求された内容を機能展開していくことで、最適な部品や手法を選ぶ。どのような設計方法で、製造プロセスで、その場合のメリット・デメリットはどうなのか。設計思想が見えるようになると一人ひとりの意識が変わってきます。今まで個人技術で見えなかった設計思想や能力が身に付き、コスト、納期順守率などを考えながら、改善の話ができるようになります。
また懸念事項に関しては、こういう設計方法の場合、こういったトラブルが予想されるという事前の対策を盛り込みましょう。これが本には載っていない自社の設計技術として意外と役立ちます。失敗事例からも学ぶところは大きいのです。
生産技術における技術伝承の進め方
最後に技術伝承のポイントを簡単に説明します。ここでご紹介するのは、生産技術におけるベテラン技術者がどうやって物事を決定しているか、そのプロセスを見るものです。
ベテラン技術者には職人技と呼ばれる部分があります。彼らが物事を知覚・解釈・判断する着眼点はどこにあるのでしょうか。
まず知覚については、設計情報や製品情報、工程管理における品質や出来栄えなどをどのように知覚しているのか。これを具体的に整理してみます。さらにどう解釈したのか、どんな風に結論づけて決定したのか。この3要素に分類しながらベテラン技術者の見える化を進めて行きます。そして、その内容を経験知、手法知、暗黙知に分類して共有化して行きます。それを総合して手法知にまとめていく。このような技術伝承の方法があります(図3)。
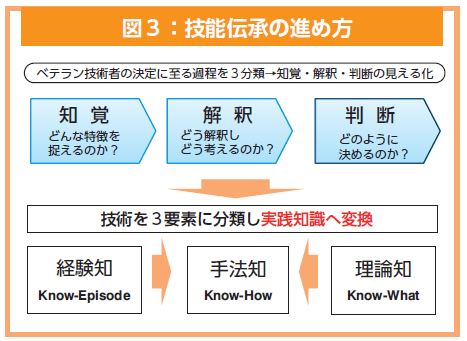
結果を導く原理原則を整理する。技術を伝えるということは理論と経験知をしっかり伝えるということです。経験知は理論を補完する重要な要素。例えば、失敗したときの経験がどういう状況で生じたのか。これを学ぶだけでも新たな気づきが生まれます。
特にミドルから若手社員に多く見られる意識の低下、これを危惧されている管理者の皆さんも多いようです。国内で勝つには技術力の向上が重要です。過去と同じ問題が何度も繰り返されていませんか。技術力が低下すれば品質の作り込み、コストの作り込みが抜けていきます。他社より技術力が落ちれば、コストや品質で劣勢に立っていく。コストや品質を上げるにはここを上げるしかありません。
このようにA社では現状の間接・直接部門の改善余力を把握して、向かっていく姿を全員で共有する“ 活人化プロジェクト”で低コスト高品質のものづくりを進めておられます。