2011.08.18
在庫最適化という難問 震災に学ぶ製販の連携と絆
- 関連タグ:
-
- 現場改革・生産性向上
- 問題発見力
- 人材育成
- 部門間連携
- 工場レイアウト
- 設備保全
- 在庫削減
執筆者:
東北大震災から、はや五ヶ月が過ぎました。政治の混乱をよそに被災地では必死の思いで復興の努力が続いています。私たちはこの過酷なまでの災害から多くの事を学びつつありますが、これらのいくつかをまとめれば、①人の傲慢と油断の危うさ、②知恵を使うことの大切さ、③人の連帯と絆の大切さ、ではないでしょうか。
実は、ものづくりの基本である、在庫最適化を行う上でも、これらの学びは大変貴重な教訓となりました。これらについて、これを機に少し解説してみたいと思います。
在庫管理における人の傲慢さと油断の危うさとは
多くの製造業では、高度な生産管理システムの導入と運用が進み、生産管理を担当するスタッフの負荷が減って、事務処理の自動化が著しく進展しました。
しかしながら、処理の自動化は進んだものの欠品の増加、在庫の増大に悩まされている企業は後を絶ちません。何故でしょうか?
理由は明白です。そもそも生産管理システムというものは、マスターデータが正しくなければ、正しく機能しないものであることは周知の通りです。
第一に考えられる理由は、購買リードタイム、論理在庫等の基礎データが現実に合っていないことが原因です。ある企業では、市況に合わせてマスターデータ精度を維持管理するというバックヤード価値業務を失っていました。それらの付けが需給バランスが乱れたこのような時代に回ってきているのです。
また、第二の理由は、生産管理システムの設計論理が、依然として、在庫引当て方式から脱却できていない、という点です。
そもそも、すべての企業が在庫ゼロを理想として、ここを目指してきたのに、ゼロになる在庫から製品、部品を引当てるという考え方自体に変化がないことが矛盾そのものです。営業、製造部門を問わず、在庫があれば勝手に先取りして引当ててしまい、何時使われるのかの確証もないまま、ただ論理在庫のみが一人歩きをしているシステムが目立ちます。このような未引当て論理在庫基準で計算されるシステムでは、もはや実在庫を最適化する能力はありません。
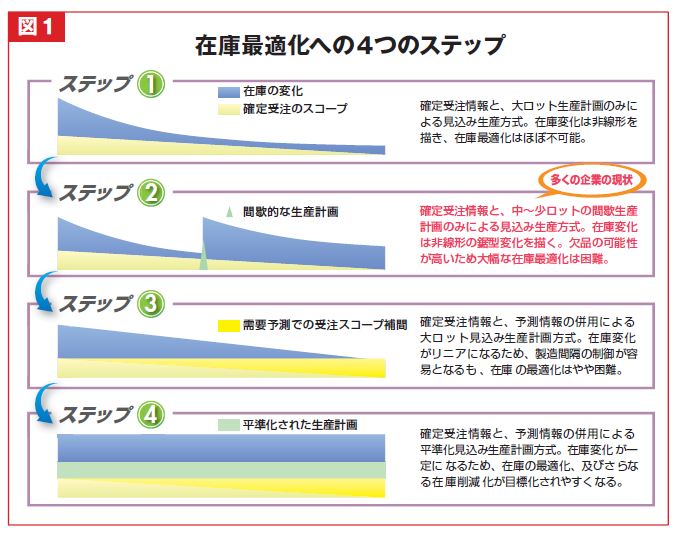
ある企業では、製品の在庫引当てを廃止し、在庫動態表なる管理ツールを用いて、実在庫の最適化、最少化を実現しました。
この時、「在庫」とは、引当てる対象ではなく、需要変動を吸収するバッファに過ぎないという意識変革を行い、実際に引当てを行う対象として、予め予測した「出荷見込数」からのみ行う事としました。
引当てた製品は、確定出荷数として、出荷見込数から減じられますが、確定出荷数と見込数の合計は、常に一定に維持されています。
そのため、未来の任意の時点で、生産計画から出荷見込数と確定数を減じた予測実在庫数は、一定となります。
否、未来実在庫が一定となるよう、生産計画を調整していると言った方が正しい表現です。
営業は営業で、製品を現在庫から引当てておく必要がなくなり、動態表の出荷日に該当する出荷見込残から、引当てることが常時できるようになります。
出荷日で引当てができるということは、納期回答を即時にできることであり、顧客への信頼性向上は計り知れないものがあります。
このような在庫動態管理ツールの原理は簡単であるものの、使いやすさを追求する企業の知恵が凝集されて、はじめて独自のノウハウとして確立されます。ここに従来の既成概念にとらわれない改善の出しどころがあるのです。
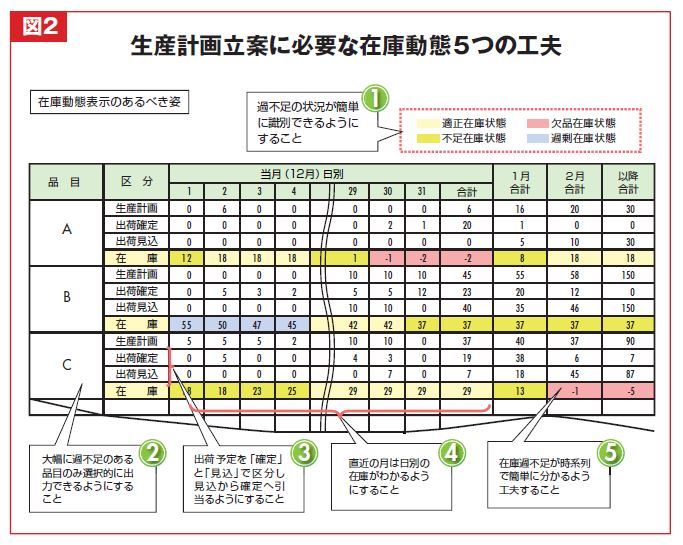
在庫管理における人の連携と絆の大切さとは
在庫最適化をテーマに社内プロジェクトを実践しようとすれば、少なくとも製販の連携と強調が必須であることは言を俟ちません。
全体最適を行うルールとしては、在庫の責任は工場責任とすることを奨めています。 工場は独自の判断基準を基に、営業からのフォーキャストを評価し、生産計画に反映するようにすべきです。
すなわち、営業情報の精度に比例した生産計画を立てるようにします。
営業は、自らの営業情報の精度に従ったリスク、すなわち若干の欠品リスクを覚悟しなければなりません。これが責任分担を介した対等で平和な、強い絆の組織関係を創り出すのです。
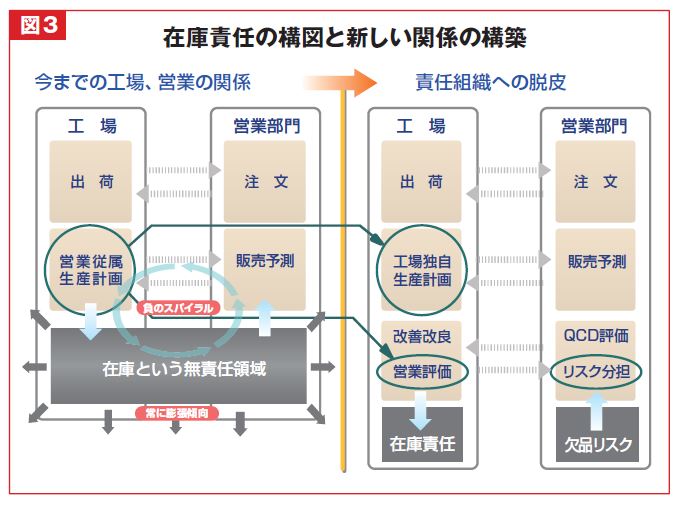