現状打破のための3つの課題
製造業への就労者人口がなかなか増えない中、需要だけが増加し、現場では慢性的な人手不足が続いています。そして、完全失業率は減少し続け、派遣社員などの非正規雇用者の確保も大変な状況になっています。
ある企業では、現場の班長が頻繁に入れ替わる派遣社員の教育に追われるばかりで、満足に監督業務が出来ずに疲弊しきっていました。本来、現場で生産性を上げて欲しいベテラン社員が、日々の生産を維持することに注力しなければならない、そのような状態が多くの企業で散見されています。
また、鋼材不足に代表されるモノ不足、貿易摩擦に端を発した中国経済の失速、製造業を取り巻く環境が大きく変化しています。こうした現状にどのように対応していけばよいか、現状打破のキーワードとして下図の3つの課題を取上げたいと思います。
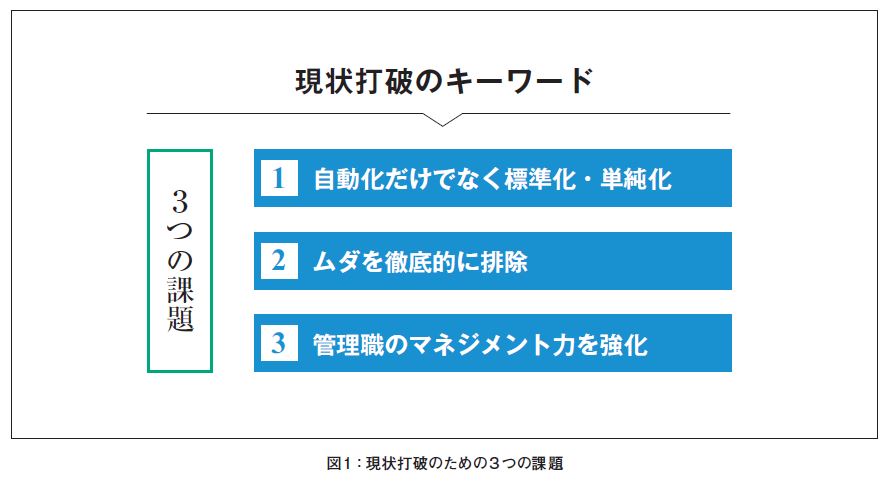
1 自動化だけでなく標準化・単純化
どこまで自動化を進めるか
人手不足の対策として自動化が有効であることは言うまでもありません。しかし、自動化は全体最適の視点を持ち、徹底して行うことが重要です。
人手で行っていた複数の加工職場を1つの設備に置き換え、省人化を図ったというケースがありました(図2)。しかし、複数の前工程職場からモノが集まって来て(合流)、複数の後工程職場にモノが供給される(分岐)状態が発生し、かえって生産のリードタイムを伸ばさなければならなくなり、工程間在庫が増えてしまいました。その結果、工程間在庫を置くスペースが増えただけでなく、運搬や移動といったマテリアル・ハンドリング(マテハン)が増え、期待通りの効果が得られませんでした。こうした現象は、高価な設備を導入した企業でよく見られます。
また、単に加工時間の部分だけの自動化が行われ、ワークの投入や排出、運搬具への積み下ろしにまで目が向けられていないということはないでしょうか。中途半端な自動化で作業者が付かなければ動かないという状態は避けたいものです。
目先の工数削減にとらわれることなく、前後工程までを含めた全体のモノの流れまでをつぶさに検討し、作業のデザインを行うことが真の自動化と言えます。
標準化・単純化の考え方
自動化と並んで人手不足の対策として挙げられるのが多能工化です。私はこの多能工化の考え方を変えていく必要があると考えています。これまでの多能工化では、「誰もが何でも出来るようになる」ことが目的と考えられています。しかし、ただでさえ負荷の高いベテラン作業者の時間をこれまで以上に教育、指導に充てることには限界があります。また、入れ替わりの激しい非正規雇用者を早期に戦力化していくことも同時に考えねばなりません。
そのためには、一連の作業内容を細かく分解し、特別な技能を要する要素とそうでない要素に分けるということが重要です。特別な技能を要する要素が隠れていると、その作業、その工程自体が難しいものと捉えられ、多能工化が図り難い、教育がし難いものとして敬遠されがちです。しかし、細かく分けることで特別な技能を有する作業者が全てを行わなくても作業が出来る可能性があります。
たとえば、大型コイルに線を巻きつけるという巻線作業では、どれぐらいのテンションを掛け、どれぐらいの回転スピードで線を巻いていくのか、全ての作業条件を定量化できれば良いですが、コイルの径であるとか、線の太さであるとか、バラツキ要素が多く、どうしてもベテランの経験に頼らざるを得ません。しかし、コイルを巻線機に上げ下ろしをするとか、次のコイルや線を準備するといった作業は安全喚起を含む作業手順とタイミングさえ教育すれば、経験の浅い作業者でも実施することが可能です。
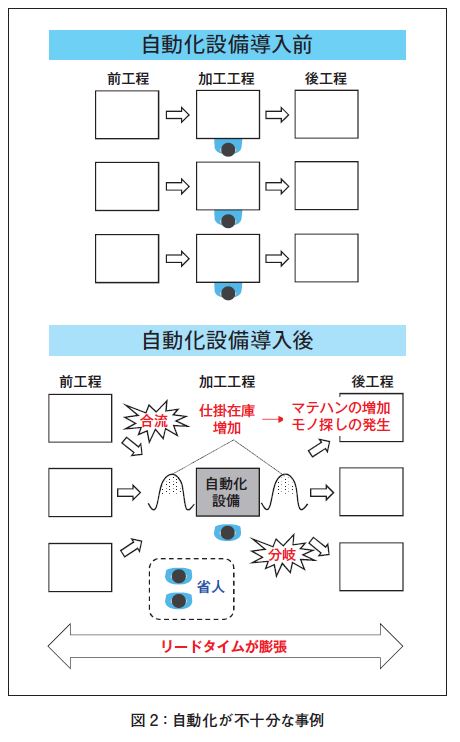
2 ムダを徹底的に排除
ムダ作業を価値作業へと転換する
VPM(Value Producing Management)では、人の作業を価値作業、準ムダ作業、ムダ作業、に3分類しています。そして、改革・改善活動では、準ムダ作業を減らし、ムダ作業を無くし、価値作業の割合を高めることで生産性向上を図ります。
機械操作や溶接作業といった価値作業は楽に早く正確にできるようにする。今の作業条件化ではやらざるを得ない検査や運搬などの準ムダ作業は出来るだけ減らしていく。さらに、手待ちや打ち合わせといった何ら付加価値に繋がらないムダ作業は無くしていく。少ない人員で利益を創出するには、この価値作業比率を高めるしかありません。
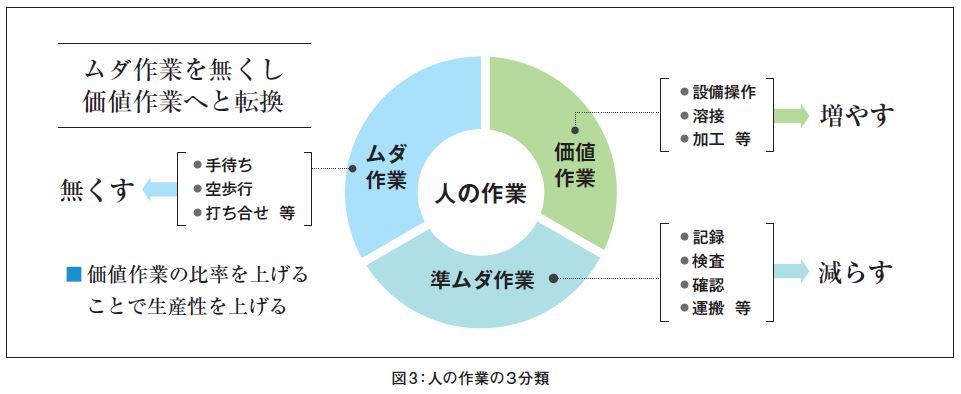
マテハンは合理化のフロンティア
自動化はマテハンを考慮して進めるべきと先述しました。モノづくりでは出来るだけモノを動かさなければ効率的ですが、現実はそうはいきません。工程と工程の間の運搬、工程の中でモノだけが動いている(ローラーなどで自走している)状態、あるいは作業者が直接モノを動かしている(取り付け取り外し等)状態などがあります。
このマテハンが生産のリードタイムに占める割合には驚かされます。一般的な企業で6割から7割も占めるからです。このマテハンに着眼し、改善することで工場の生産性を上げることが可能です。
先日、ある自動車部品メーカーでワークサンプリングを実施したところ、価値作業の比率が28%、準ムダ作業が56%、ムダ作業が16%という結果になりました。ムダ作業の比率が準ムダ作業のそれを下回るのは、お客様に鍛えられている業界ならではかもしれません。そして、準ムダ作業、ムダ作業の中味を分析すると、準備作業、積み替え作業、手運搬や台車運搬、フォークリフト運搬などの運搬作業、運搬の合い間にある空歩行といったマテハンが26%も占めていました。このマテハンを10%でも改善して価値作業にすれば、この企業は1.3倍の生産性を上げることが出来ます。
バトンとバトンゾーン
改革・改善活動において、目に見える作業のムダに気づくことは比較的容易です。しかし、工程間在庫の膨張によるマテハンの増加といったムダは、仕事の進め方の悪さに起因するものであり、なかなか発見しづらいものです。私はこうしたムダを「しくみのムダ」と呼んでいます。
企業や工場は多くの部門、工程を情報やモノといった「バトン」が渡っていき、仕事が成り立っています。最終的にお客様からお金をいただくまで、さまざまな人の手をバトンが渡っていきます。社内で上手く「バトンリレー」が出来ているか、しくみのしっかりとしている企業では、部門や工程間(バトンゾーン)でリズム良くスピードを落とさずにバトン渡しが出来ています。皆さんの会社ではバトンゾーンで上手く「バトンリレー」が出来ているでしょうか。
バトンゾーンの中で、渡し手は受け手のことを考えてバトンを差し出し、受け手は渡し手が渡し易いように手を差し出す、前後の部門、工程がいかに協働体制を築いてパフォーマンスを高めるか、これが「しくみのムダ」を改善するポイントとなります。
改善効果を経営成果へと確実に転換する
ここまでムダを徹底的に排除することについて述べてきましたが、ムダを排除して生まれた改善効果を経営成果へと確実に転換することが重要であることは言うまでもありません。そして、テクノ経営では成果をしっかりと刈り取ることを大事にしています。
たとえば、QCサークル活動や5S活動で「歩行を3歩減らした」、「1個当たりの生産時間を0.5秒短縮した」という発表があります。それを金額換算して月1万円の改善効果が生まれたと言っても、実際に会社の金庫に現金が入る訳ではありません。勿論、こうした改善を否定する訳ではありませんが、我々が取り組むべきは、改善で生まれた効果を経営成果へと変えることです。
そのため、VPMには「負荷投入バランス調整」というしくみがあります。これは負荷(仕事量)に合わせて工数を掛けるもしくは保有工数に合わせて負荷を調整する、ということです。当然ながら改善を行えば工数が下がることになりますが、工数が下がった分だけ仕事量を増やすか、人を出すか、コントロールを行います。そして、空いた工数が発生した場合に備え、事前にどうコントロールするかを先に考えておくことが重要です。ただ「改善せよ」と言うだけでなく、生産性が130%に上がったらどれだけ工数が空くか、それをどう活用するかを考えておかねばなりません。
3 管理職のマネジメント力を強化する
目指す姿を共有し、課題解決に向けて行動する
ヒト・モノ不足という環境変化に対応するために組織のパフォーマンスを上げなければならない。そのためには管理職のマネジメント力をより強化することが求められます。
ある企業で部課長職のマネジメント力を強化するために、自分の組織の3~5年後の目指す姿を描いて貰っています。この姿を描くためには現状をしっかりと把握していなければならず、かつ上位の方針を十分に理解し、自らの組織の機能を明確にしておかねばなりません。部課長が目指す姿を示せなければ、部下には未来が描けず、パフォーマンスも上がりません。そして、目指す姿が鮮明になれば、それを達成するための障害要因(課題)が見えてきます。
一方、自らの組織の当たり前の水準を高めることも重要です。正常な状態(決め事が決まっている状態)が無ければ異常は見えず、問題解決の行動が取られません。まず、決め事を決め、それを守る/守らせる、決め事が守られているか確認する、その上で決め事を改善するという日常管理のサイクルをしっかりと回していくことがマネジメントの基本となります。
おわりに
以上、ヒト・モノ不足に対応するための現状打破の3つの課題について述べてきました。
日々発生する問題の対処に追われ、改革・改善活動を行う間も無いという言葉を耳にすることが数多くありますが、日々の行動を「考働」に変えるだけで上記、3つの課題の解決に繋がっていきます。何よりもまずやってみようという姿勢で取り組んでいただければ幸いです。