本ページでは、アマテイ株式会社様に対するコンサルティング実績をご紹介しています。
日本における釘の歴史は古く、法隆寺金堂から飛鳥時代の和釘が用いられていたことが確認されており、これが日本で使用された中で最古の釘と言われている。その後明治時代初頭までは和釘の時代が続くが、日本の近代化と共に建てられるようになった西洋建築には、接合力の弱さから和釘では対応できなかったため、欧米から洋釘が大量に輸入されるようになり、次第に和釘は淘汰されていった。明治41年には国策として釘の安定供給を図るため、官営八幡製鉄所が釘の材料となる線材の生産を開始、洋釘が国内生産で賄えるようになった。このような日本における洋釘の黎明期に創業し、以降一貫して洋釘の製造・販売を専門に事業展開するのがアマテイ株式会社である。その長い歴史の中、常に時代の要請に先んじた開発力で、洋釘製造のリーディングメーカーとして業界を牽引してきた同社ではお客様のニーズに応える高品質で特殊な製品を開発し続けることで、更なる成長に向けた歩みを確実に進めている。今回の企業インタビューではアマテイ株式会社における改善活動の取組みを生産本部 常務取締役 後藤 哲也氏、生産管理部 次長 中野 守氏、生産管理部 開発Gr長 狭間 貴博氏からお話を伺った。
(※ASAP 2019年 2号より抜粋)
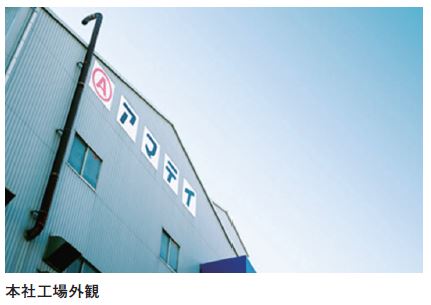
釘一筋118年の歴史と高い技術力を源泉に成長
まず御社の会社概要についてお伺いできればと思います
後藤: 明治44年(1911年)、日本で2番目の製釘工場として尼崎に設立された岸本製釘所が当社の起源です。以降、尼崎の地理的な利便性を活かし、時代や経済情勢の変化による影響を受けながらも、今日まで釘一筋で第一線を走り続けてきました。現在は日本で使用されている釘の8割が輸入品と言われており、市場としては非常に厳しい状況にありますが、このような情勢においても、長い歴史の中で培ってきたノウハウと技術力をベースに、営業と生産が一体となってお客様ニーズに沿った製品の開発を行うことで、品質面、開発面で国内外の競合他社との差別化を図り、優位性を生み出しています。高い評価をいただいているコンクリート釘や、当社のオリジナル釘「木割れ最強釘」など、既存の釘に留まらない、釘の可能性を今後も追い求め、常に新しい製品を提供し続けていきたいと考えております。
尼崎工場はどのように運営されているのでしょうか
後藤: 現在は製造部門が57名、出荷部門が8名、事務部門が15名(内11名が生産関係)合計80名の体制で運営しています。従業員は基本的に正社員での雇用とっており、専門性の高い技術を持った人で、65歳以上の方も在籍されています。雇用状況としては一時期、離職率が高く、たえず募集をかけて、新しいに人に入ってもらうような状況が続いていましたが、現在はすこし落ち着いています。正社員で長く働いてもらっている人は会社としても安心して仕事を任すことが出来るので、定年以降も一部雇用を延長して働いてもらっている人もいますが、やはり将来的なことを考えて、自動化などの取組みも推進しています。
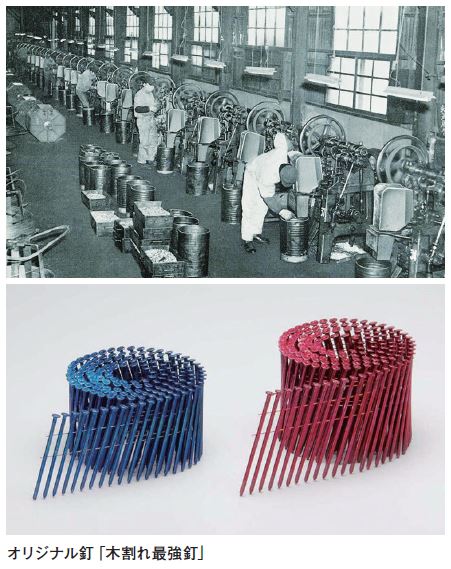
人の行動に着目した改善活動「VPM」に対する期待
今回の改善活動の導入の経緯について教えてくだ さい
後藤: 2013年為替変動以降、当社におけるOEMと国産のシェアが逆転したため、国産の生産能力アップを図るために新設備を導入することになり、それを機として工場改善プロジェクトを立ち上げました。プロジェクトでは総合効率を上げること、能力アップに注力して、生産能力もかなり向上しましたが、ほぼ上限に近いところまで達成して、頭打ち・マンネリの状態になってきたため、別の視点、切り口によって、さらに能力アップが出来ないかと検討していたところ、テクノ経営から紹介された改善手法が人の行動に着目する「VPM」でした。これまでの工場改善プロジェクトでは設備効率、保全体制を中心にやってきたため、この新しい視点の改善手法に興味・関心を持ち、2017年の4月から数ヶ月間をテスト期間として、導入を検討することにしました。その上で、工場全員のベクトルを合わせるために何度も改善活動の導入について話し合い、最終的には全員の合意を経て、コンサルティングの導入を決定しました。コンサルティングの費用対効果の算出は難しいですが、当社としては導入した以上は必ず数字での成果を出すことが必要であり、文字通り不退転の決意で活動をスタートしました。
中野: 自分の中でのコンサルティング導入についての印象は、これまで行ってきた工場改善プロジェクトが頭打ちとなる中、新しい手法があればまだ向上させることができるのではないかという期待が一番大きかったと思います。工場改善プロジェクトも5年目となっており、手法、ネタももう出尽くしたような状況だったので、コンサルティング導入はちょうど良いタイミングだったと思います。
狭間: 人の行動への着目というのは、あまりにも当たり前すぎて、今まで自分にも、会社にも無かった視点でした。特に人の行動を、「価値作業」、「付帯作業」、「無価値作業」の3区分化することで、改善対象である付帯作業、無価値作業を明確にして、作業方法の見直しで人の総合効率を改善する手法は斬新だと思いました。この手法に乗ってみるかという感じでした。
VPMによる人の成長を実感することが出来た改善活動
改善活動を進める上で苦労されたことは
中野: 会社としても生産能力を最大にしていく方針で、現場では作業をしながら、改善活動を行わなければならない状況でした。一方で生産能力を上げながら、改善活動の内容も覚えないといけない状況で、現場の作業員の負担はかなり大きかったと思います。また活動の核であるVPMは参加者全員に発言を求めるのが基本ですが、当社の現場作業員は基本的にはあまり自分から発言しない人が多いため、当初は現場の作業員に意見を聞いても、なかなか答えが返ってこない状況が続いため、少し苦労しました。本当にこれで改善活動を進めることが出来るのかと不安になったこともあります。
活動を推進する中で社員の変化はどうだったので しょうか
中野: 現場の社員は活動当初からこの18ヶ月間で大きく変化、成長したと思います。これまでは部と言いながらも個人で仕事をしていたような感じだったのが、毎朝の「C改善」活動などを通じて、徐々に部としての横のつながりが出てきて、それが活動に対する現場の変化のきっかけになったと思います。そして活動が進む中、今まで社内でほとんど発言や提案をしたことがない人から、積極的な意見などが出るようになり、現場が活性化していきました。普段なかなか自分の意見を言わなかった現場の作業員が、自分の意見をしっかり話せるようになったことは人材育成の面からも大きな効果があったと感じています。これまでのプロジェクトと今回の活動の違いは、現場が自分たちの活動と捉えていて、活動に対する「やらされ感」というのが感じられないことです。以前の活動はどちらかというとトップダウン型で、こちらが指示することへの反発もありましたが、今回の活動では逆に現場からこんなことがやりたいという相談を受けることもあります。そういう意味ではボトムアップ型の活動と言え、会社全体の底上げにつながったと考えています。
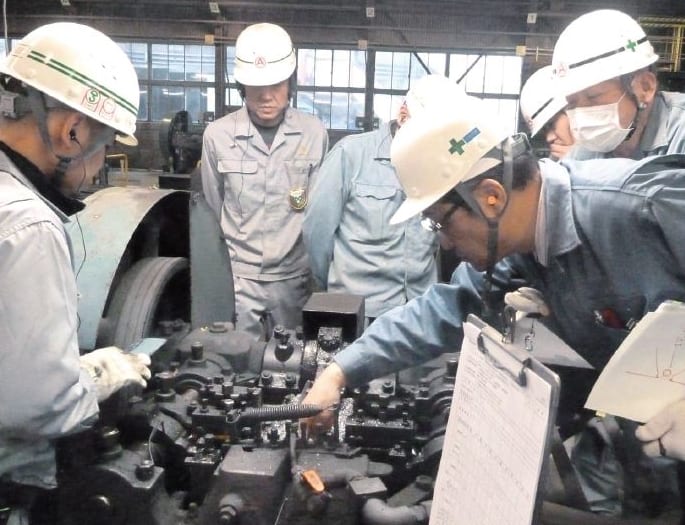
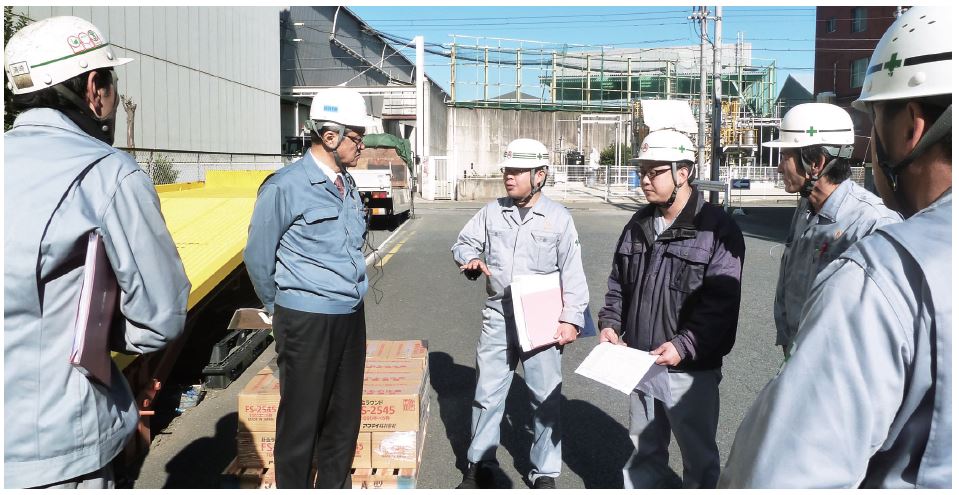
その変化を生み出した一番の要因はどこにあると思われますか
後藤: VPMの素晴しさは参加者全員が納得して取り組める手法であることだと思います。私はこれまでの経験で全員参加の改善活動と謳いながら、実際にはそれを実現することの難しさを充分理解しています。強制的に参加させた形だけの全員参加の活動でなく、敷居の低いテーマ設定で、知らず知らずの内に自発的な全員参加を実現するC改善活動が現場社員の変化を生み出した源であると思います。当社にはお取引先など様々なお客様が来られますが、お客様が工場の掲示板などで改善活動に興味を持たれた際にVPMにおけるC改善についてお話させてもらっています。全員参加のC改善活動をベースに『固定観念を打破し仕事のやり方を抜本的に変えるD改善活動』へスムースに移行できたと思います。
改善活動によるアマテイの企業風土への影響はあったでしょうか
中野: 今までは基本的に部署間のつながりが少ない状況でしたが、この活動の後は他部署の主任同士で打合せをしたりして、横のつながりが出来てきました。これまでは、部署間の作業について、それぞれの作業内容への理解不足から言い争いになったりすることもありましたが、それはお互いの事情や仕事の内容を知らないから文句が出たりしていたのであって、この活動の発表会で隣の部署の苦労などを知ることで、それらは自然と解消されて、コミュニケーションが活性化したと思います。当社の現場担当者は20代の若手社員から60代のベテラン社員まで年代も幅広く、これまではコミュニケーションを取るのが難しい面がありましたが、この活動を通じて必然的に話をする機会が増え、仕事以外でのコミュニケーションも活発になり、企業風土は良い方向に進化したと思います。
活動の具体的な成果はどのようなものだったのでしょうか?
後藤: 活動をスタートした2017 年7月の総合効率(価値時間/投入時間)16.46%をベンチマークに目標はベンチマークの25%UP、すなわち20.58%に設定しました。2018 年の一時期、地震や大型台風による被害で総合効率が停滞しましたが、2018 年11月に総合効率は目標を上回る22.07%(34.1%UP)に達しました。同月開催された全社発表会では総合効率が34.1%改善し目標の25%を大きく上回ったこと、さらに「線釘」「第一加工」「第二加工」「物流」の各工程からD改善活動の事例報告が行われました。また、毎日15分実施してきたC改善活動件数は累計2,492 件となりました。
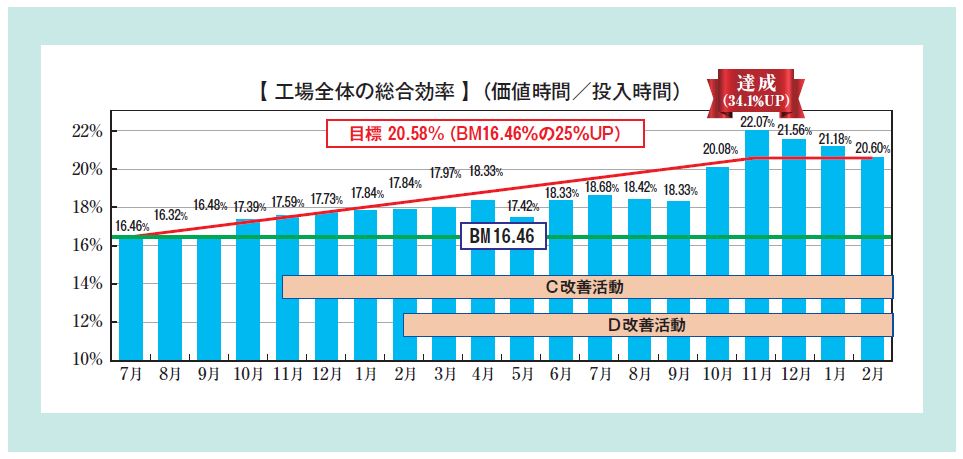
活動に参加された社員の感想はいかがでしょうか
中野:
活動に参加して「良かったこと」としては
・VPMを取り入れたことで改善活動を全員参加で行うことの大切さを理解した
・改善することの楽しさを知り、班員全員が積極的に参加するようになった
・目標を決め活動を続けた結果、メンバー間の結束力が強くなった
などがあり、この活動を通じて現場の結束力、全員参加での改善活動の重要性への認識などが高まったことを示していると思います。
また「苦しかったこと」としては
・班員に講習で習った内容をうまく伝え、理解、浸透させるのに時間がかかった
・仕事をやらされているという意識から、自分達がやってやるという意識の改革
・大きな改善活動を実施する場合、各自の考えが異なるため同じ方向に向かうのに苦労した
などがあり、活動を進めるためのコミュニケーション、班員のベクトルを同じ方向に合わせることの難しさなどが共通の声として聞かれましたが、全ての部署が今後も改善活動を続けていくことを明言しており、活動スタートから18ヶ月間でよりポジティヴな活動へと進化していったことを示しています。
今後の活動で注力していきたい取組みについてお聞かせください
後藤: 基本的な方向性として、さらに生産性を上げていく中で、色んな局面に柔軟に対応できる生産部門を目指して行きたいと考えています。また今後の人手不足問題や働き方改革への対応を視野に入れ、より少人数で生産する方法の検討を進めて行きます。この取組みについてもVPMを核とし、自動化など新しい生産技術とのマッチングを図ることで、作業者が納得し、もっと楽になる生産を目指して活動をさらに進化させていきます。
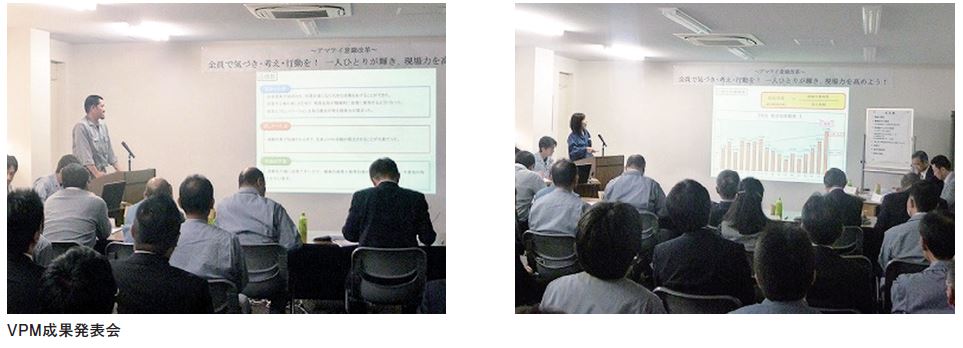
生産の中長期でのビジョンについてお聞かせください
後藤: 今後の活動と重なる部分がありますが、将来的な無人化、省人化に対する設備投資も行っていきたいと考えています。今後も、生産と販売のバランスを見極めながら、無人稼動の時間を拡大させていくとともに、人手を必要とする物流や梱包、検査、工程についても、順次無人化に向けた検討を進めていきます。ものづくり企業である当社としては、自動化でただ人を減らせば良いということではなく、技術はしっかりと残しつつ、ブラッシュアップして熟練工から次世代へ継承していきたいと考えています。
本日はありがとうございました。
取材にご協力いただいた方
アマテイ株式会社
生産本部 常務取締役 本部長 後藤 哲也 氏
生産本部 生産管理部 次長 中野 守 氏
生産本部 生産管理部 開発Gr長 狭間 貴博 氏