北アルプス・立山連峰を望み、蜃気楼の見える街「魚津」。幻想的な光を放つ春の使者ホタルイカや縄文杉が眠る埋没林の存在は海外からも知られる存在だ。山と海の距離が近く、海抜2400mから富山湾の水深1000mという高低差。急峻な地形がもたらす豊かな地下水と自然の恵みが彼の地では生活の基盤となっている。
その魚津の地に創業した日本カーバイド工業(ビニフレーム工業の親会社)は、機能化学品、機能樹脂、電子素材、フィルム、ステッカーなどの幅広い分野の製品づくりを進める企業。今年で86年の歴史を持つ。
ビニフレーム工業は、日本カーバイド工業のグループ企業として昭和37年(1962)に設立された。当初はプラスチック建具・襖のパイオニアメーカーとして誕生。その後、アルミ建材メーカーとして、国内アルミ産業の発展に歩みを合わせながら数々の商品を世に送り出してきた。作図から生産までのオーダーメイド商品や自社規格品では、あらゆるニーズに対応できる多品種少量生産の生産体制を有し、また高い機能性が要求される樹脂商品では、最新の押出成形技術により樹脂サッシ部材やLED照明用カバーなどの生活を豊かにする商品を製造。設計から金型製作・試作・量産までを一貫して社内で行っている。
「存在感のあるキラリと光る会社」を提唱する同社のコーポレート・スローガンは社名であるビニフレームの頭文字からとった「VF」 それは、Vision to Future 想像~創造へ(一歩先んずる発想)を意味する。これからも将来のビジョンに向かって、数々の商品を通じて未来を創造し続けていく。
社長就任後に、まず考えたこと
コンサルティングご導入の経緯についてお伺いいたします
新夕氏:
当社の親会社である日本カーバイド工業では、約6年前からテクノ経営のコンサルティングを導入して社内の改善活動を進めてきました。ちょうど私が日本カーバイド工業の魚津・早月工場長に就任したときに、その改善活動は2年目に入っており、前任の工場長に代わってその後の活動をプロジェクトリーダーとして引き継ぐことになりました。
それまで魚津・早月工場では、ともすれば井の中の蛙に陥りがちなところ、その現場での直接指導が刺激となって改善活動は盛り上がり、非常に高い活動成果を出すことができました。ご担当をいただいたテクノ経営の手島先生には大変お世話になったと感謝しています。
その後、私はビニフレーム工業の社長に就任して、当社が抱える課題とその克服に向けての方策を考えていましたが業績向上のためには、工場を大きく改革する必要性を強く感じるようになりました。日本カーバイド工業での経験から、現場指導というコンサルティングのスタイルであれば活動成果が出やすいということが分かっていました。ボトムアップの意識が現場に根付きましたし、勉強会や研修に参加したりするなかで私自身の考え方も変化したところがあります。それでビニフレーム工業の社長就任後、ぜひ当社でも同様の活動を実施したいと考えました。
どちらかというと自分の方から積極的に取り組みたいというのが私の性格というか、モットーです。そこで木下取締役と金森工場長に相談して導入を進めることにしたのです。
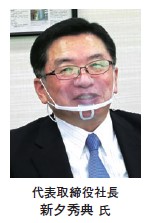
工場診断を受けられてのご感想はいかがでしたか
新夕氏:
もともとコンサルティングをお願いするつもりでしたが、最初のステップが工場診断からなので、現状分析をしっかりやっていただきました。
当社に足りないところは私自身も理解していましたが、診断の結果もほとんど同じで想定の範囲でした。
ところが分かっていても自分たちでやろうとするとなかなかできないものです。やはり説得力のある第三者の視点でみんなに教えてもらって、それで一緒に進めるというのがいいだろうと思っていましたので、過去の経験から日本カーバイド工業で指導いただいた手島先生にご担当いただくことになりました。
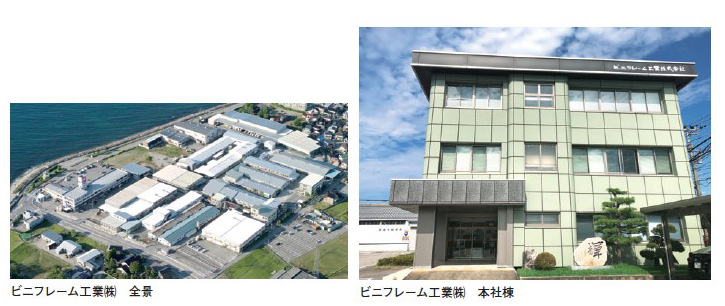
工場が抱えておられた課題は何でしょうか
新夕氏:
当社には建材工場と樹脂工場があります。建材工場ではビルやマンション、一般住宅などで使われるアルミ製の手すりや笠木、カーポートなどの一貫生産を行っています。
また樹脂工場では押出成形技術を用いた様々な商品づくり、営業や技術担当がお客様のご要望を伺い、設計から金型製作・試作・量産までを社内で行える体制づくりをしています。
当時の課題は、樹脂工場の生産性があまり良くなく、業績も低迷していたことでした。それで工場診断も、まず樹脂工場を対象に実施してもらうことにしました。
ところが工場診断後のプレゼンテーションで活動プログラムの説明を受けたところ、「これは樹脂だけじゃなくて建材も一緒にやった方がいいんじゃないか」と思い、木下取締役と金森工場長に相談したところ2人とも同意見だったので、「それじゃ樹脂だけじゃなく、全社的にやろう」ということになりました。そして、その結果として建材工場も改善の成果が伸長する状況になりました。
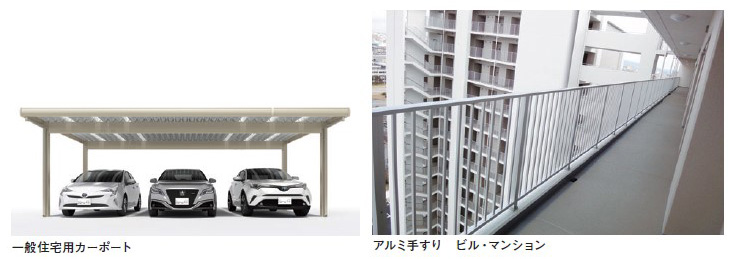
コンサル導入について、現場の抵抗感はありませんでしたか
新夕氏:
確かに当社の場合、外部コンサルタントの活用は初めてでした。だから私もそれを一番心配していたのですが、ここでも木下取締役と金森工場長の2人にはちゃんと理解してフォローしながら進めてもらいました。
現場メンバーには活動の主旨をしっかり理解して、取り組んでもらわないと困ると思っていましたが、当社の従業員はみんな真面目で予想以上にしっかりと取り組んでくれました。私の心配は杞憂に終わったようです。本当に真剣に取り組んでくれて感謝している、その気持ちは毎回の推進会議で伝えるようにしています。
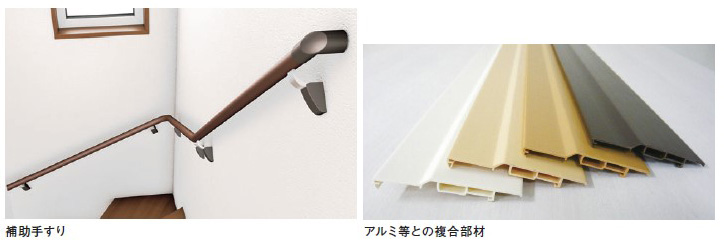
社長様が毎月の会議に参加されることはすばらしいですね
新夕氏: 従業員の皆さんがしっかり取り組んでくれているので、毎回出席してコメントするようにしています。
木下氏:
コンサルティングの経験がなかったので、少しは抵抗感もありましたが、正式にスタートしたところ、最初のカリキュラムが「気づき」であったことがよかったと思います。まず気づいたことを紙に貼って出す簡単な活動。誰でも抵抗感なく取り組めるところが功を奏しました。
ミ-ティングで現場メンバーと話をしていると、いまでも気づいた部分を即、記入して壁に貼るという「気づき」を継続しているチームがありました。それを見れば「気づき」には発展する余地がまだまだあるのかなと思います。先ほど新夕社長もおっしゃいましたが、当社の従業員は皆さん真面目なんですよ。
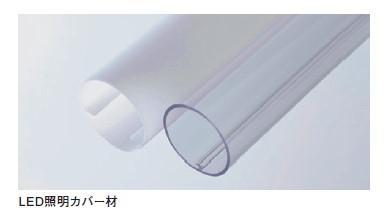
「気づき」からはじまった改善活動
改善活動の名称について教えてください。
木下氏:
活動の名称とスローガンは、キックオフ式典の前に社内で募集しました。集まったアイデアについて審査を行いまして、「改善∞(見つけ)隊」という活動名としました。無限大マーク(∞)は双眼鏡のイメージで、改善を無限に見つけ出していこうという意味を持たせています。
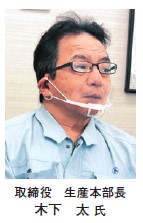
活動チームの構成はどう進められましたか
木下氏:
スタート時には建材製造グループと樹脂製造グループを合わせた12チームで活動を開始しました。
その後1年経過した現在では9チームがさらなる改善を進めている状態です。先ほどお話した「気づき」をきっかけとした日常改善である「C改善」、横断的テーマで取り組む「D改善」と活動の幅を広げています。
今では活動に慣れ、楽しみながら取り組んでいる姿が見られるようになりました。推進会議や活動報告会などの発表資料も徐々にステップアップして、今では動画なども積極的に取り入れて活動を進めています。
※C改善:「Change&Control」
毎日の作業実態の中から問題点を見つけだし、解決をはかっていく改善アプローチ
※D改善;「Design&Development」
作業方法・設計仕様・製造工程の中に潜む潜在的ムダを追究し排除していく改善アプローチ
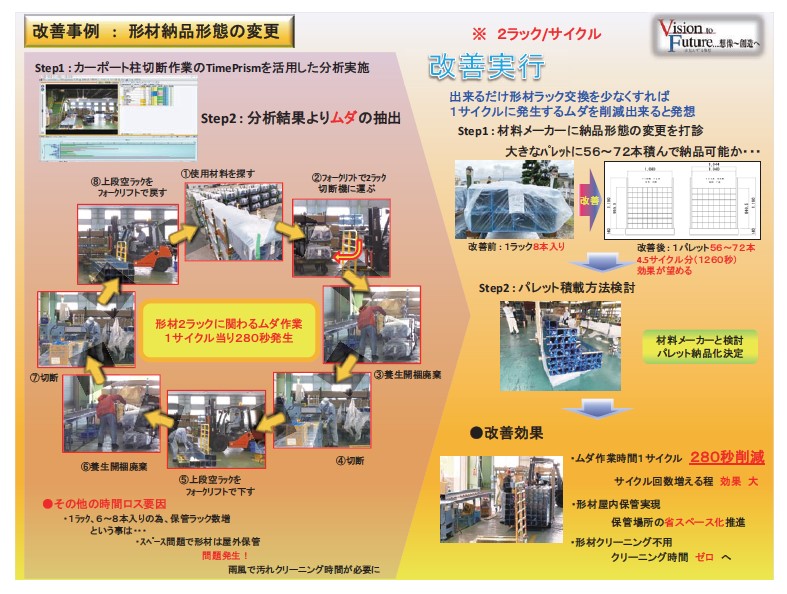
改善活動の進め方についてお伺いします
木下氏:
まずキックオフ式典で正式に各チームがテーマと目標値を決めました。その後、毎月2回のコンサルティング会合を行い、その中で推進会議も開催しています。
活動目標の設定について工夫されたことは
木下氏: 活動目標はキックオフ式典のときに、各チームのスローガンということでリーダーに宣言していただきました。たとえば「我々は生産性何%アップします」「何%コストダウンします」など、全社的には10~20%の生産性向上の目標がありますが、それに基づき各チームが宣言する目標値を色紙に書いて新夕社長に提出しました。
改善テーマの設定については現場の視点でないとわからないところがありますね
新夕氏:
その通りです、木下取締役と金森工場長の2人はある程度分かっているんでしょうけど、本当に現場の人にしか分からないこともありますし、その作業をしている人にしか分からないこともあるんですよね。
一つは手島先生にちゃんと現場に入ってもらって、現場を見てもらって、その都度実践しながらやってもらっている、「この作業はいらないね」とか。直接現場で指導してもらっていることが私は一番よいと思っていますし、現場の方も手島先生の話をよく聞いて真摯に取り組んでくれています。まずはやってみようというスタンスで取組んでいるのが良いようです。
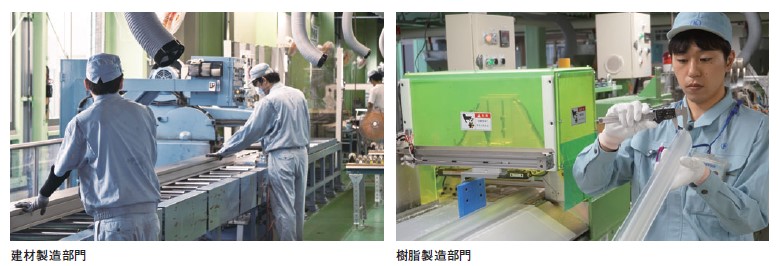
動画を活用した作業分析に取り組まれているそうですね
新夕氏: 当社では、動画解析ソフトを作業改善に活用しています。最初は一部のチームだけが使っていたのですが、それを推進会議で全チームに紹介して、今では全チームに横展開しています。
木下氏:
動画で作業分析をすると、作業を実際に撮影している人もそれを見ている人も気づく。そして作業分析の目的について考える力も養えます。この作業は何秒、ここは何秒という計測から、ムダ時間はここだと発見する。そんな風に自分たちで考える力がついてきました。そういう意味でも動画活用は効果的でした。
1年目を終えての活動成果はいかがでしたか
木下氏: ある程度、目標値を達成しているチームもあれば、まだ80%というチームもあります。また改善対象アイテムの変更などの状況により、新たなテーマを設定して対策を取る場合もあります。それらを平均しても、成果的には80%は達成していると考えています。
新夕氏: 目標値に対しては80%ですが、実際の改善効果にはそれ以外の部分もあります。たとえば工場が目に見えて綺麗になりました。とてもすっきりしたなと感じています。これも動線や作業のしやすい効率的な環境づくりを考えて改善を進めてきた結果ではないでしょうか。
木下氏:
動線改善で動きを何秒まで縮められるか。はじめは分レベルで考えていたのが、秒単位の積み重ねで緻密に考えられるようになりました。
トータル的な作業時間を短縮するという発想では、段取り改善に取り組むチームもあります。作業分析で前段取りを見直したり、工具の位置などを検討して動線短縮を図りました。
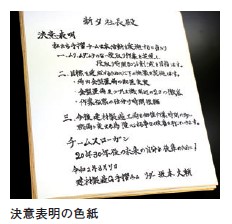
2年目を迎えた改善活動について
2年目に入っての変化点、1年目と違うところは
木下氏:
1年目は、まずチームの基礎を固める時期。誰をリーダーに選んで、継続的に活動を推進できるかどうか。心配事もありましたが、金森工場長と相談しながら進めました。実際にやってみなければわからない部分もあります。スタートした当初は不安もありましたが、キックオフ式典に続いて、気づき、C改善、D改善、推進会議などを続けながら各チームメンバーを牽引するリーダー自身も成長しました。大きなトラブルなく、楽しんで改善を行う職場風土が生まれましたので、それを引き継いで2年目の新たな目標を再設定しました。一部継続中のものもあれば、新規のテーマもあり、スムーズに進んでいると思っています。
しかしながら一部のチームでは、まだまだ目標値に到達できない悩みがあります。それについては、手法や考え方を手島先生から指導いただいて取り組んでいます。
金森氏:
重複した話かもしれませんが、1年目と2年目との差、その一番大きな違いは現在、9チームで約80 名のメンバーが活動していますが、それぞれの成長が千差万別だということです。社内には若い人は少ないのですが、当社では20 代、30 代のメンバーを若年層と呼んでいます。
彼らと個別にいろいろと話をする機会がありますが、特に2年目になってからは彼らの言動が大きく変化してきました。先ほども木下取締役が話しましたが、1年目の活動を基礎活動。基礎から始まって、ある程度の目標値・目標項目を立てられるようになったのが2年目です。
2年目になって若年層のメンバーが「どうやったら儲かるんですか」とか「工場長、僕のやっているこの仕事って実際に儲かっているんですかね」と、そんな問いかけをするようになったのです。これはかなり進歩しているなと思いました。それで「1秒1円なんだよね」「10秒でもムダをすれば、これは10円の損をしているんだよね」と返しましたが、彼ら自身も間違いなくコストを意識して話をしていました。
そういう若いメンバーもいれば、まあ中年、といったら失礼ですが50代くらいのメンバーからも「今まで人づてに継承された、段取り、加工のやり方で、ずっとやってたんですが」「こういう風に変えたいんです」という積極的な意見がミーティングで聞かれるようになりました。今では1秒1円というコスト感覚で話ができるようになり、そういう会話が休憩時間に普通にでてくるようになりました。
当社の活動のなかに5S発表会があるのですが、改善∞隊のロジックを5Sで発表するネタづくりにそのまま活用するメンバー、ちょっと編集しながら活動に取り込むメンバーもいます。こうした応用技、ものごとの筋立ての仕方ができるようになりました。発表の内容もすごく分かりやすくなったという副次的な効果もあります。1年目と2年目の変化点というのはそのあたりではないでしょうか。
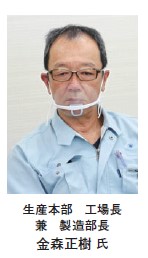
今後の改善活動や会社の発展に向けたお考えはいかがでしょうか。
新夕氏:
とにかくまだまだ生産能力を上げられると思っています。課題はいくらでもあります。生産性を倍増させるために、投資的な側面と作業改善の両輪があります。
投資の部分は会社としてしっかりやっていきますし、かつ現場での作業などはしっかりこの活動で励んでもらって、到達点として会社としての生産能力の向上を目指していきます。
それと活動は継続が大事なんですね。継続しながら皆んなで目標を共有して、目標に向かって全員で進むという形でやっていきたい。
木下氏: 目標に向かって改善を継続することで、個々のチーム、個々の人材が底上げしながらボトムアップでいろんな意見が出せるような体制を作りたいと考えています。3年目に向けては状況を見ながら、さらなる生産性アップを考えて計画していきたいと思っています。
金森氏:
そうですね。いま2年目で製造現場の改善はかなり進んできました。チームリーダーにもモノづくりの知識もかなり備わってきました。今後は、営業からの注文があっての製造部門ですので、営業から生産までのロジック、サプライチェーンなど、そういった今まで経験のない部分を製造のメンバーの知識として勉強してもらいたい。新たな知識向上につながるような活動をしてみたいですね。
どうしても単に造るだけだと、そこで線を切ってしまいそうなところがありますので、モノを造って、それをお客様にお届けするまでのロジックですね。仕入れもそうですが、サプライチェーンなど、ちょっとその辺の知識を与えてあげたい。そうすればモノづくりの本質がトータルに理解できると思います。そこまでもう少し突っ込んでやってみたい。
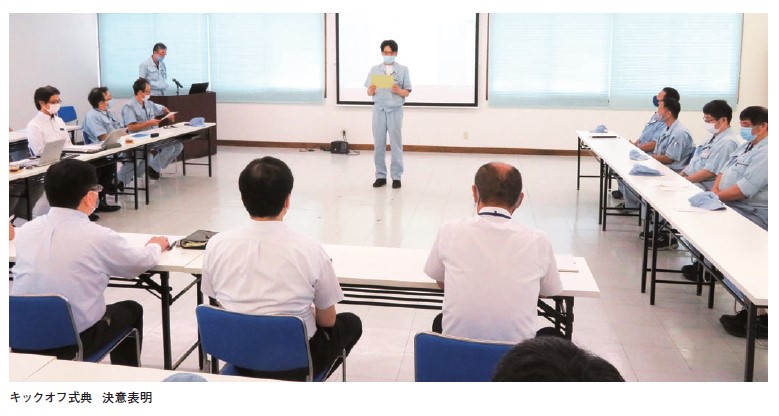
最後にお聞きしますコンサルティングって儲けにつながりますか。
新夕氏: 私はつながると思いますね。こういう言い方は一般的ですが、やっぱり企業は人だと思っていますので、一人ひとりのスキルがアップすることで間違いなく、企業の利益は上がると思いますね。そう信じてやっています。コンサルタントの手島先生も、そうした私の考え方に理解を示して一緒にやってもらっているので助かっています。
本日はありがとうございました
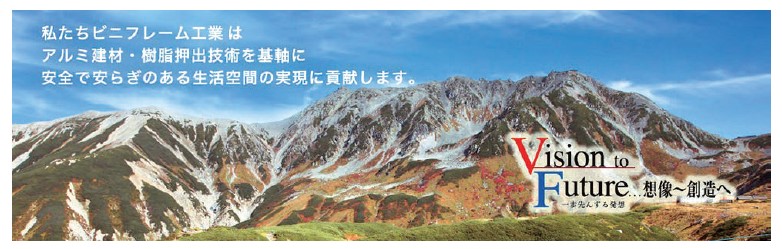
取材にご協力いただいた方
ビニフレーム工業株式会社
代表取締役社長 新夕 秀典 氏
取締役 生産本部長 木下 太 氏
生産本部 工場長 兼 製造部長 金森 正樹 氏
PDFダウンロード
【コンサルティング事例】 ビニフレーム工業株式会社様