上下水道、電気、ガス、道路、線路、通信網など、私たちの生活や産業を支えるたくさんのインフラ設備。その中で、電気エネルギーの輸送に使用される絶縁電線を衝撃や張力から保護するだけでなく、ゲーブルそのものの保護や美観の向上、隠ぺいに用いられるのが電線管である。大別すると金属製と合成樹脂製の2種類がある電設資材で、こうした電線管の設置に欠かせないものがコネクタやボックス、カップリングなどの付属品だ。材質や形状など、あらゆる用途に合わせて、その種類は多岐にわたる。
電成興業株式会社は、1950年(昭和25年)に電線管およびその付属品の販売を目的に、当初は商社として設立され、以降は時代の要請に応じながら、電線管付属品を全般的に製造するメーカーへと変貌を遂げた。70年以上の伝統と実績を誇り、全国にわたる幅広い営業地域と、自社ブランドの製品を素材の加工から表面処理まで自社工場で一貫して生産できる強みを活かし、中小企業とはいえ、暮らしや社会、産業活動に不可欠な配電インフラ事業の一翼を担う企業として今日まで成長を続けてきた。
こうした中、これまでの現場ありきといった生産方式からの脱却や組織体系の確立、マネジメント力の強化、そして何よりも『自分達が誇れる工場にしていきたい』という強い想いを掲げ、新たな体制へと生まれ変わるべく導入された同社の活動について、常務取締役 工場長 丹沢 康祐 氏、副工場長 部長 舟橋 浩 氏、生産管理課 係長 丸木 翔太 氏、品質管理課 主任 阿部 雄太 氏からお話を伺った。
(※2023年 ASAP+ 3号より)
自社工場での一貫生産を強みに事業を展開
御社の事業内容についてお聞かせください
丹沢氏: 1950年(昭和25年)に祖父が創業した会社で、当初は電線管や付属品を販売する商社、いわゆる材料屋として始まりました。その後、祖父の出身地である山梨に工場を建設し、電線管の付属部品に関する製造を開始しました。埼玉へ主力工場を移設した後、徐々に事業を拡大していきながら、JIS表示許可工場(第366200号)としての認定を取得し、1989年(平成元年)には山形の酒田へ主に板金関係の特注品を取り扱う新たな工場を立ち上げました。現在は、JIS規格となる電線管の付属品に加え、板金関係の特注品や溶融亜鉛めっきなどの表面処理を主な事業としています。
御社独自の強みはどういった部分にありますか
丹沢氏: 材料の購入から表面処理、販売まで、多少は外注も使用しますが、ほぼ一貫して社内で生産できるところが弊社の強みですね。鉄の板物関連から樹脂、ダイキャスト関連の鋳造、射出成形の樹脂関連も取り扱っています。あとは表面処理、電着塗装や溶融亜鉛めっきなどのめっき関連と、もう一つ大きいのが金型です。金型も社内で製造、メンテナンスを行っています。ここまで対応しているところはなかなか無いと思うのですが、そこをすべて社内で取り扱っているため、生産面では融通が利きますし、品質面は一貫して管理ができます。さらには金型のメンテナンスも社内で対応しているため、トラブルが起きても、早急に解決へ向けて動けますし、費用的な部分でもメリットが大きいということが弊社の優位性になると思います。
自意識改革や改善活動の推進力が課題
弊社のコンサルティングを導入する前に、どのような課題をお持ちだったのでしょうか
丹沢氏: 私が入社して20年ほどですが、当初は組織体系が整っておらず、生産では受注残が出ていたり、品質面でのクレームも多かったりという状況で、その場しのぎでやっているような感じでした。私自身、以前は家具の金物関連を製造・販売している会社で設計や生産技術などの業務に携わり、ある程度は製造業を学んでいたので、正直最初は「よくこれで生産できているな」という印象でした。そこから、生産管理や品質管理といった間接部門の設立と強化に取り組みました。その後、徐々に人員を増やしながら何とか組織として形作ることができたのですが、現場の長をはじめ、皆の意識が変わらなければ改善していくのは難しいという段階に来ていました。
舟橋氏: 私が入社したのは今から40年以上前になりますが、当時を振り返ると現場を含め、3S、5Sといった片付けが基本でした。工場はモノを作る所で、現場ではケガなどの危険性もあったため、整理整頓は大切な部分でしたが、全体の人数に対して管理する部門の人数が圧倒的に少なかったですね。そういう状況の中、生産管理から品質管理など、とにかく兼任のような状態で、あらゆることに対応し、本当に苦労していました。
丸木氏: 入社当初は間接部門の人数自体が少なく、トラブルが起きたらその対応に追われることの繰り返しで、前に進んでいる感覚が全くありませんでした。ようやく人数が揃ってきて、改善活動に向けて少しは前進し始めたのですが、今度は実行に移す時間の捻出や現場の協力も難しく、苦労しました。1年、2年と改善活動は続いていましたが、結果が伴わず、非常にもどかしい日々が続いていましたね。
阿部氏: 品質管理課として入社した後、最初の1~2年は応援人員として金型や出荷センターで働いていました。現場はかなり汚れていて、作業場所にはいろんなものが乱雑に置かれており、結局応援にいっても最初にやることは必ず3S、清掃だったことを今でもよく覚えています。現場は3Sの重要性が分からないわけではないのですが、そのやり方を上手く伝えられないような状態が続いていました。
分析や評価の数値化が印象的だった1日工場診断
弊社の1日工場診断を受けた印象はいかがでしたか
丹沢氏: 「何が普通なのか」ということを、皆が認識しなければいけないと感じており、テクノ経営さんに1日工場診断をお願いしました。診断結果を分析し、数値化して提示いただきましたが、現場の評価をどのようにすべきか悩んでいましたので、基準を作って数値化し、評価を行っていく部分が非常に良かったですね。現場に対してどのようにモチベーションを高めていくかという課題に対しても、生産性の評価や現状把握、また達成感という部分にもつながるような内容で、「こういう形で実現できるのか」と感じ、ぜひやりたいと思いました。
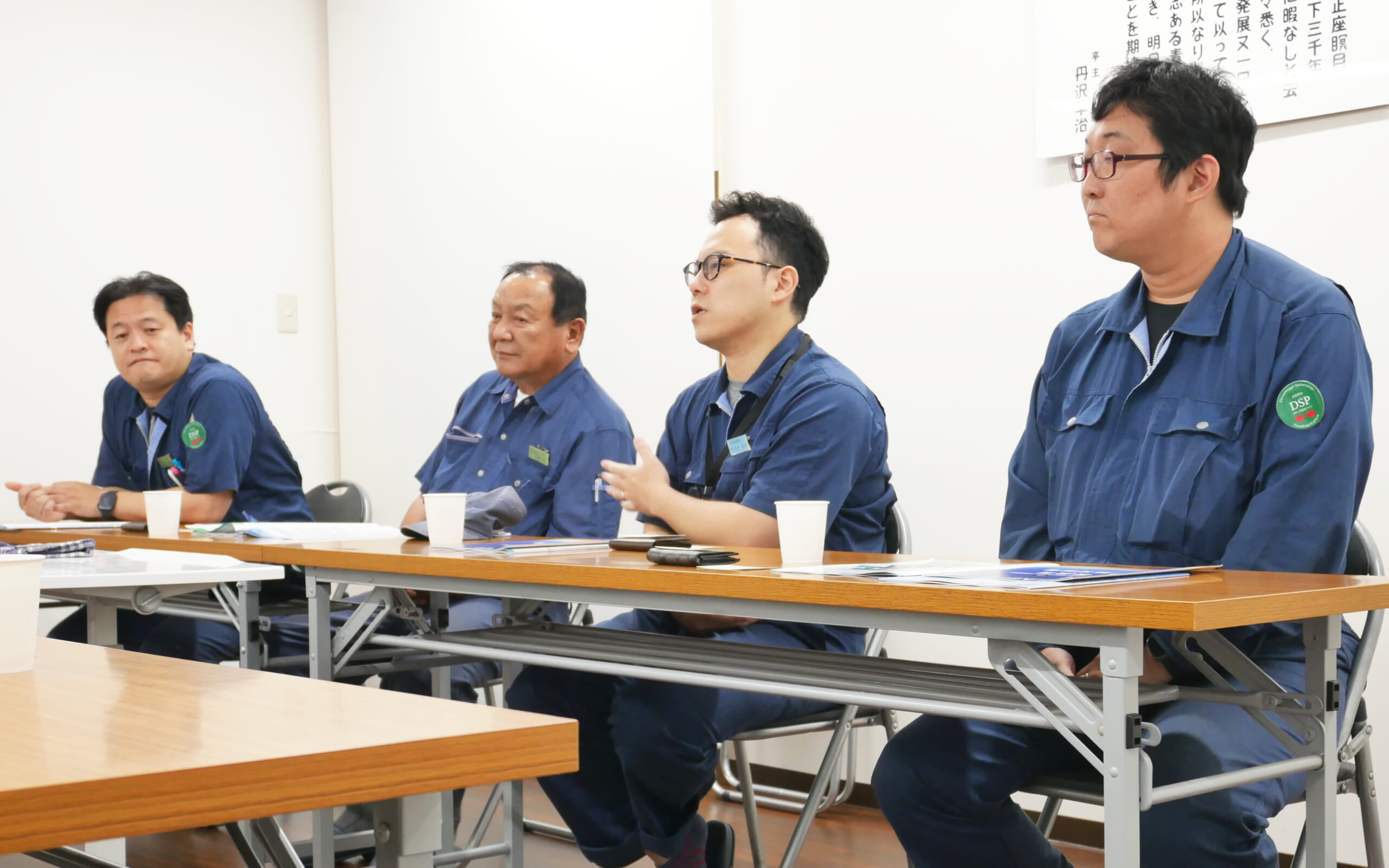
コンサルティング導入の決め手はありましたか
丹沢氏: どれだけムダなことを行っているのか、またどれだけ伸び代があるのかといった部分をご提案いただき、実施する価値があると思いました。コンサルティングを導入するにあたって一番求めていたことは、現場の意識を変えて、マネジメント力のある組織体系を作り上げることでした。間接人員の組織はある程度作ってきたのですが、10ヵ所ほどある製造現場の組織改革には至っていませんでした。トップダウン的な生産で、指示を待つだけの人員が増えてしまい、自ら考えて行動できなくなっていた印象です。そのため、改善活動を実施しようとしても、人任せというか、いくら間接人員が頑張っても全く活動が前に進んでいかない。組織として非常にまずい状況で、これを変えていくにはどうしたらいいか悩んでいました。そういった部分で、現場のリーダーが自ら考え、マネジメントできるような意識改革を実現したかったのも導入を決めた理由でした。
丸木氏: 社内で話し合って「こういう風に改善活動を進めていこう」と決めても、間接部門だけでは根本的な解決にならないというのは長い期間ずっと実施してきて分かっていたことでしたので、外部の力を借りないと難しいと感じていました。時間は有限ですので、結果が出ないまま日々が過ぎていくことに焦りもあった中、コンサルタントを導入してはどうかという工場長の発案に対しては賛成でした。
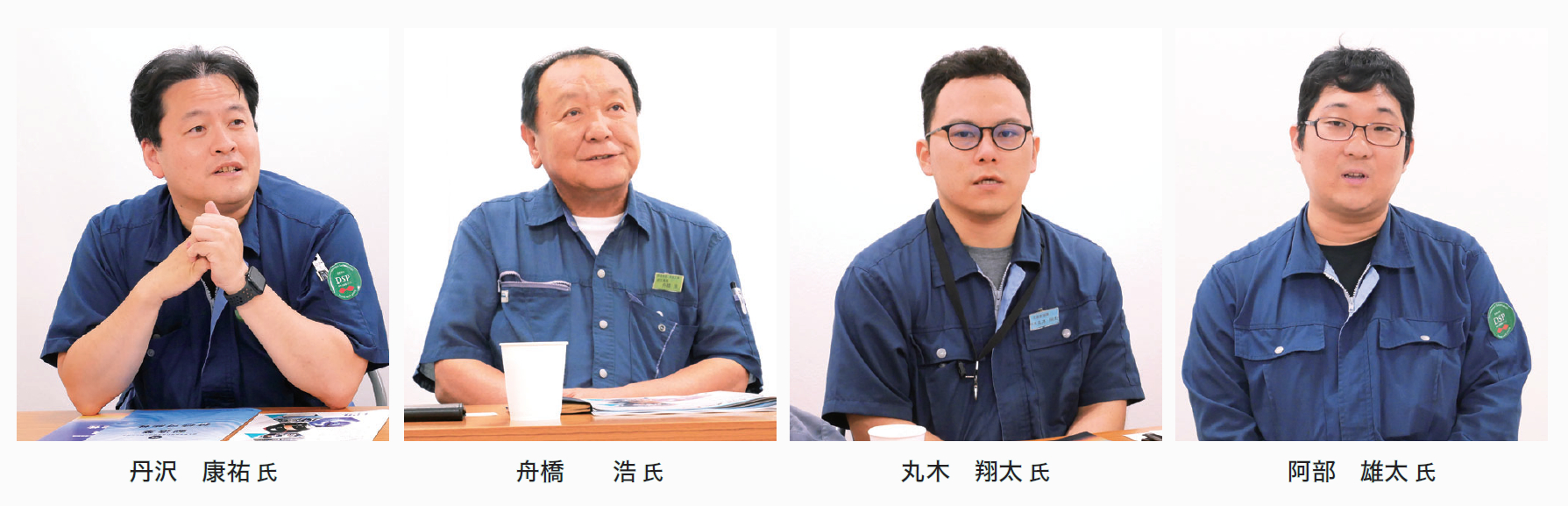
仲間はおらず、手探りで始めた導入当初
コンサルティングを導入した当初はいかがでしたか
丹沢氏: 一番大変だったのはこの2人(丸木氏、阿部氏)だったと思いますよ。私が決めたのですが、2人を専任メンバーに抜擢し、活動を進めてもらいました。もちろん、将来的にはこの工場の中心メンバーになってもらいたいという期待もあって決めたのですが、やはりこういった活動を経験することや、プロの方に見てもらって、その知識や経験を吸収することは大きな成長につながりますので。もともと頭の中には実現したいイメージがあって、その方向性を決めていくのが私の役割でしたが、実際に現場を巻き込みながら進めていくのはこの2人でしたので、本当に大変だったと思います。
丸木氏: 今は軌道に乗ったのでだいぶ俯瞰してみられるようになりましたが、活動が始まった当初は本当に大変でした。コンサルタントの小久保先生から活動の方向性や期間ごとの実現すべきマスタープランを提示いただきましたが、とにかく1年目はある程度の結果を出すところまではやらないといけないので、そのベース作りが大変すぎて……。平日は遅くまで残業し、土曜出勤もしょっちゅうで、何とか指標のマスターデータやその入力用フォーマットなどを作成していました。小久保先生には「恐らく後で振り返ったら大変だったと思うかもしれないけど、できると思うよ」と言われたのを覚えていますが、それは今になってですが、確かにその通りだったなと思います。最初の基礎作りは何をするにしても初めてでしたので、とても苦労しました。現場の人もやはり全てが初めての経験で分からないことがあれば聞かれるのですが、聞かれるこっちも分からなくて。とにかく手探りで少しずつ実施していき、半年程で成果というか何となく手応えを感じ、ある程度自信につながりましたね。現場の方も、徐々に改善活動の結果が見えるようになってきて、現在に至るという感じです。
阿部氏: 導入当初で一番大変だったことは、仲間がいないというか、現場に同じ方向を向いている人が誰もいないというのが本当に辛かったです。何とか自分達と同じ方向へ振り向いてもらうのに4~5ヵ月ぐらいかかり、現場の統制をとるという意味では一番苦労しました。活動を続けていると徐々に現場もやり方が分かってきて、「こうやってやればいいのか」「じゃあ、やってみます」という声が上がり始め、今では任せていることも増えました。最初と比べると格段に違いが出始めています。
変わり始めた人と現場 自分達が誇れる工場へ
プロジェクトの名称はどのような想いから決められたのでしょうか
丹沢氏: コンサルティング導入以前から私の懸念事項として、やる気のある社員が嫌になってしまうような職場になってはいけないというのがありました。そういった意味でも、このプロジェクトの目的として、やる気のある人、向上心のある人が頑張ろうと思えるような環境づくりをしたいと考えていて、『DSPプロジェクト』と命名しました。電成興業、埼玉工場、プラウドワークプレイスでDSPですね。要するに、自分達が誇れる工場、そして希望の持てる会社にしなければいけないという強い想いがありました。不安しかないような会社では未来が無い。同じ問題を繰り返し、その場しのぎのような仕事をしているようでは、若い人材を含めて皆が嫌になってしまうと思います。だから、本当に「うちの会社は良い会社なんだ」って自慢できるような会社にすることができれば、おのずとモチベーションは上がり、良い人材も入社して定着し、皆が成長していける。そこを目指しているのですが、プロジェクトを通して、徐々にその効果を実感している状況です。
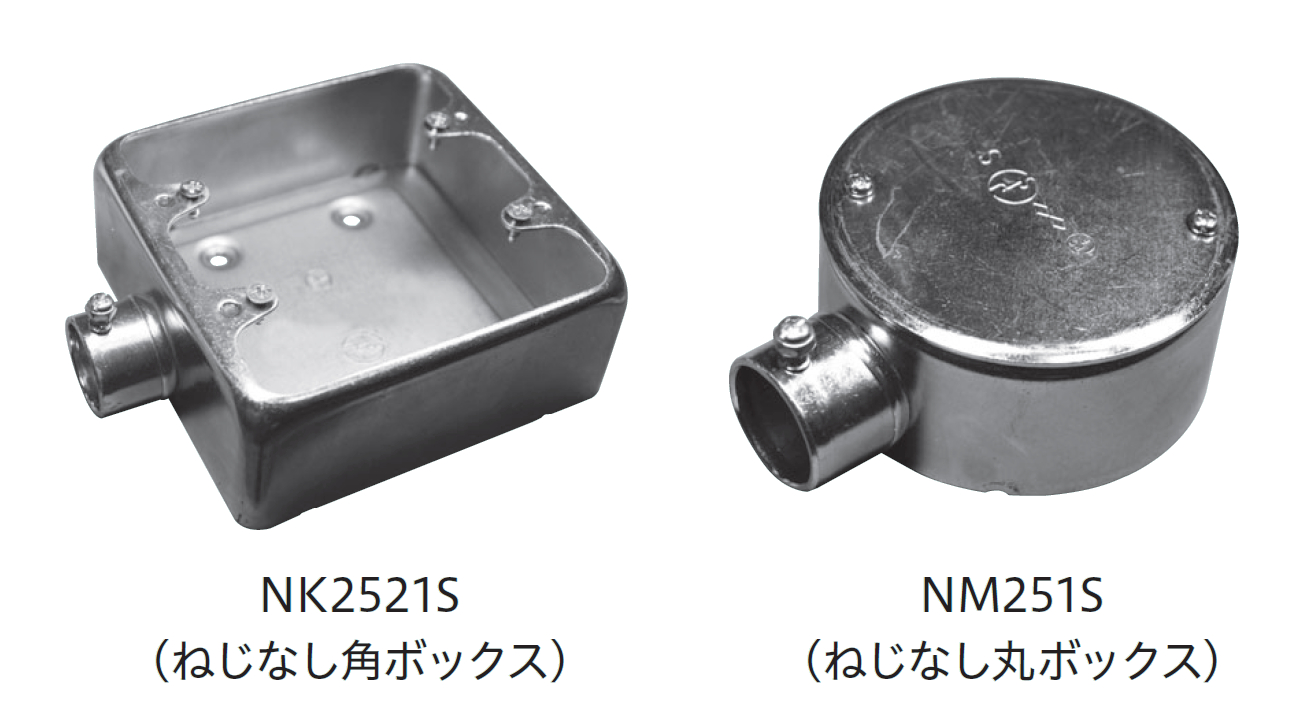
コンサルティング導入の成果をどのように実感されていますか
丹沢氏: 明らかに現場の環境が変わりました。工場として最低限、整理整頓ができていないと仕事ができないですし、安全面についても不安が残ってしまいます。そういった基本の部分をしっかりと工場全体で実践できているというのが導入当初の活動でまず実感した部分ですね。そこから、問題発見トレーニングを行い、改善活動につなげていくのですが、最初はマンネリ化していて何が問題か分からないような状態から、ちゃんと分析をして原因を追究し、さらには実際の仕事に活かしていくことで効果を実感できるところまで成長しています。導入時はリーダーだけでしたが、徐々にメンバーを含めて活動に取り組み、また他部署との交流も増えて、いろいろな発見があったと思います。若い人材を含めて、やる気のある人が仕事のしやすい職場になってきて、そういう道筋ができたことを含めて、非常に大きな効果があったかなと感じています。
舟橋氏: 明らかに良くなっているから言えるのですが、本当にびっくりするくらい変わっています。昔は会議をしてもただの報告だけで終わってしまったり、現場で生産の不良が発生すると関連部門で責任のなすりつけ合いのような状態になったり。良い品質の製品をできるだけ安価で製作することが目的なのですが、何か起きた時には品質管理部門が入るだけで話し合いもできなかった。それが今では、生産管理や品質管理はもちろん、各現場の代表が推進リーダー会議で発表し、お互いに意見を出し合い、協力しています。自分の部署以外の人と話す機会も増え、若い人達も積極的に意見を出せるような環境になり、そういったところが一番変化を感じますね。
阿部氏: このプロジェクトを開始してからちょうど1年半ほどになるのですが、最初は目に見える部分が明らかに変化し、3S、5Sというのは本当に変わりました。あとはDSPプロジェクトの中で組織された推進リーダー会議を実施するようになり、まだ道半ばではあるのですが、だんだんと間接人員と同じような感覚を持った人が出てきてくれて、かなり大きな進歩だと感じています。日報を1つ作るにしても、以前は間接人員が一から十まで全部作るような状態でしたが、今では自発的に自分達で取り組んでくれています。本当に大きな変化だと思いますね。
部門間の連携や現場の人達に変化はありましたか
丹沢氏: プロジェクトの様々な活動をきっかけに、現場の部署間での交流は増えていますね。あとはやはり推進リーダー会議かな。そこで各現場の発表を聞くことによって、他部署の状況を理解できるようになりました。お互いの事情を理解し合うことで、実際の業務に役立つような質問や、他部署の応援にいくといった助け合いも増えました。そういった意味では一体感が出てきたなと感じています。
丸木氏: 確実に変わったと実感しています。昔は、現場でモノを作っているのが正義といった感じで、あくまで生産が第一でした。そのため、生産以外の時間が割けないという文化がずっと続いていたので、話し合いの時間すら作ってもらえず、何か問題が起きれば間接人員が聞き取りに行き、それを関連する他の部署へ伝達するような状態でした。しかし、テクノ経営さんのコンサルティングが始まって、様々な活動を進める中で話し合いや会議の時間が必要になるため、ちゃんと仕事上の時間として取りましょうということになり、現場の人達も「その時間を取って良いのか」という認識に変わっていきました。それでも、最初は「生産以外のことに時間を割くのはどうなのか」という風な感情が根強く残っていた感じでしたけど、1日1時間ぐらいは打ち合わせの場を作るとか、月に1回は報告の場を作って、推進リーダー会議で発表してもらうとか、徐々に変化していきました。会議の結果を受けて、間接人員と相談して、次はどのように改善していけばよいかというのをきちんとPDCAで回していく、こうした時間を取れるようになったのは非常に大きな効果だと思いますね。
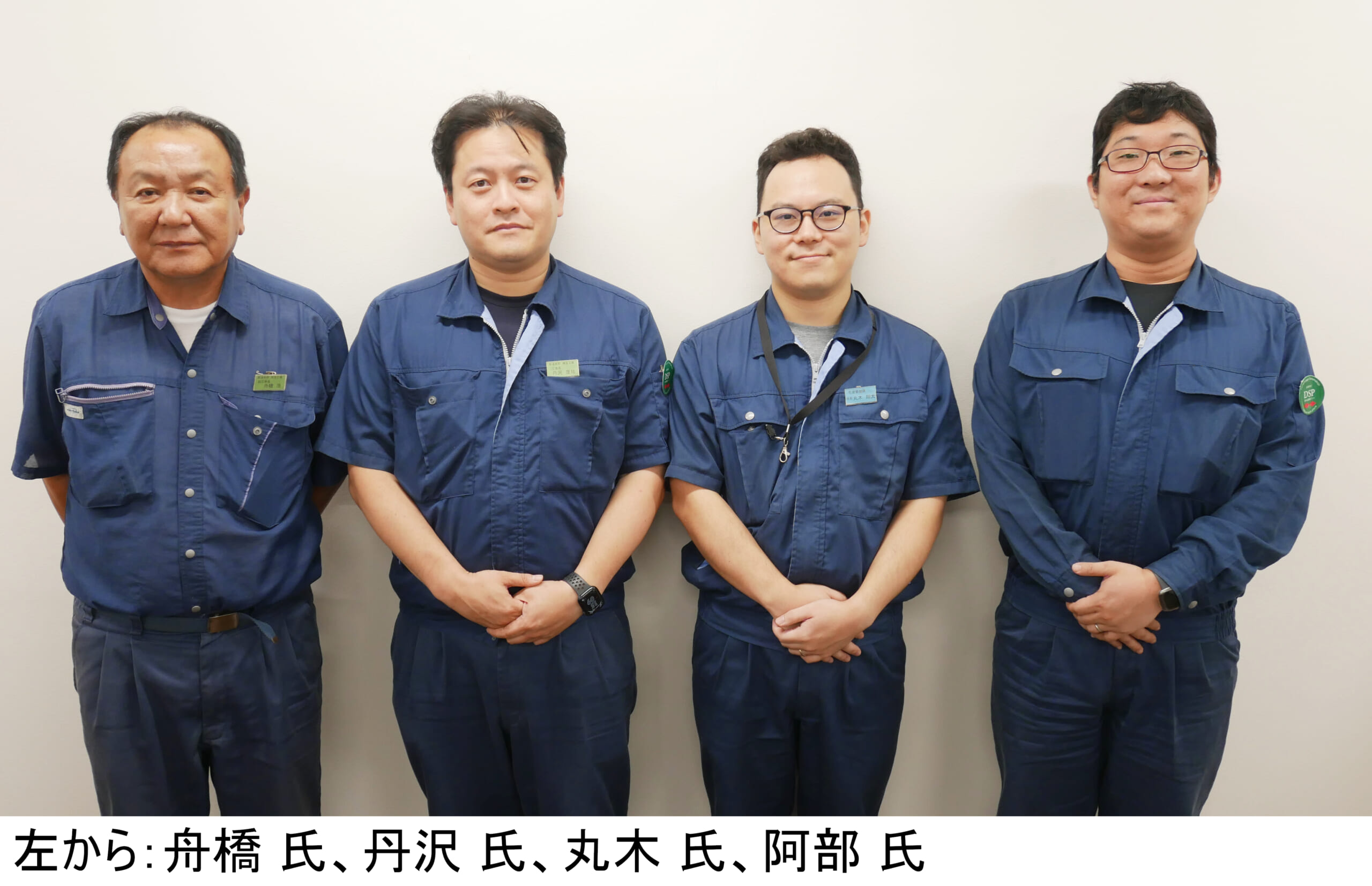
STAFF COLUMN 新たな時代への挑戦
~確かな未来を創造していくために~
常務取締役 工場長 丹沢 康祐 氏: 私が思い描いている工場の姿は、現場にはマネジメントのできる管理職が配置され、皆が、特に若い人材が希望を持って働けるような工場です。そのために、やはり人材育成と組織を体系立てていかなければいけません。頑張ればちゃんと評価され、自分の仕事に誇りが持てるように。このDSPプロジェクトは、そういう私の想いで立ち上げたのですが、実現に向けてまだまだ細かい部分、やるべきことがたくさんあります。そうした課題を克服していけば、生産技術の向上や売上にもつながっていくと思いますし、品質の良い製品をたくさん作り、お客様に提供していくといった工場の責任も果たしていける。本当に社員が希望を抱き、誇りをもって働ける環境を築き上げていきたいですね。
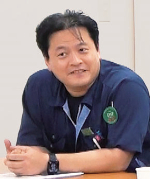
副工場長 部長 舟橋 浩 氏: まずは生産、品質、コストをしっかりと意識して取り組んでいける体制を整えること。そのためには、まだまだ間接人員が足りていないので、まずはそこを充実させるために動いてもらっています。そして現場では、このDSPプロジェクトを通してマネジメントのできる管理職をたくさん育てて、現場主導で生産管理を実施していけるようなところまで全体的にレベルアップしていきたいですね。とにかく今、テクノ経営さんの指導で本当に良い方向へ変わってきていますので、この先も続けていただき、若い人達に夢や希望を持ってもらえるような会社にしていければ最高だなと思っています。そういう姿を目指していきたいですね。
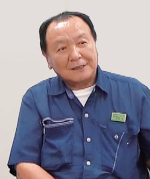
生産管理課 係長 丸木 翔太 氏: 私は所属が生産管理課になりますので、量産品の生産計画や在庫管理などを行っています。その中で、やはり一番クリアしたい課題としては欠品を減らすという点です。工場として生産性を高めて欠品を減らす目標で動いてはいますが、成果が現れていない状況ですので、まずはそこを重点的に取り組んでいきたいですね。欠品が多いと、どうしてもそれを解消するために残業が増えたり、休日出勤をしたりと、働くのが大変っていうふうになりがちなのですが、一人ひとりの生産性が高まれば、従業員も休みが取りやすくなり、ワークライフバランスという点でも整っていくと思います。そういった意味でも生産性を高めて働きやすい職場にしていけるよう、このプロジェクトを通して進めていきたいですね。
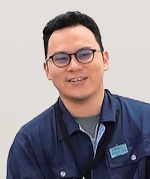
品質管理課 主任 阿部 雄太 氏: 私がこのプロジェクトを通して感じているのは、組織のマネジメントが大切だということです。形骸化したものではなく、ちゃんと各製造現場の班長や副班長がマネジメント力のある組織を目指しています。なぜなら、組織力が上がることで、以前は間接人員が全て指示していたことを自分達で実施するようになり、時間が取れずに進んでいかなかった活動もやっと取り組むことができているからです。こうした結果、管理によって発生する不良が圧倒的に激減できており、品質向上はもちろん、最終的には生産数にも良い影響を与え、品質、生産の両面を同時に達成していけるのではと考えています。ですので、まずは各班の組織力、組織としてのマネジメント力向上を目指していきたいですね。
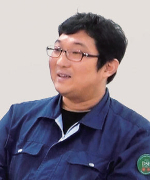
取材にご協力いただいた方
電成興業株式会社
常務取締役 工場長 丹沢 康祐 氏
副工場長 部長 舟橋 浩 氏
生産管理課 係長 丸木 翔太 氏
品質管理課 主任 阿部 雄太 氏
PDFダウンロード
【コンサルティング事例】 電成興業株式会社様