本ページでは、日本アイ・ティ・エフ株式会社 久世工場様に対するコンサルティング実績をご紹介しています。
日本アイ・ティ・エフ株式会社は、住友電気工業のコーティング技術と日新電機のイオンプラズマ技術・ コーティング装置技術を融合し設立された企業である。薄膜技術は金属を始めとする様々な材料の性能や機 能性を高める技術の一つ。表面に薄いセラミックの膜を生成し、強い耐熱性や耐摩耗性を実現する。
蓄積されたノウハウにより、他の追従を許さない多様なバリエーションを展開。同社の高品質・高性能 コーティング膜は様々な産業分野で活用されている。グローバル化や市場変化の中、地球環境に優しいセラ ミックコーティングの役割はより一層大きくなってきた。
独自の薄膜技術で未来を拓くソリューションカンパニー、技術者の努力と思いが幾重にも積み重なった分厚い技術に 期待が高まっている。
同社、久世工場では全体最適に向けた改善プロジェクトを推進、工場全員の総力を挙げて取り組んできた。 ステップアップで自他ともに★★★(三ツ星)評価される工場を目指した活動を紹介する。
(※ASAP 2015年 No.1より抜粋)
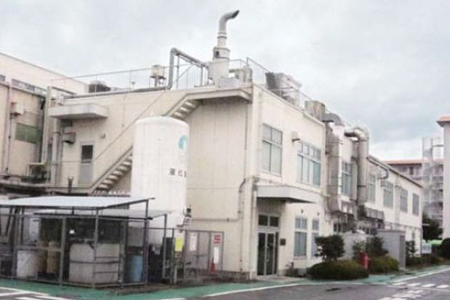
日本アイ・ティ・エフ株式会社 久世工場様
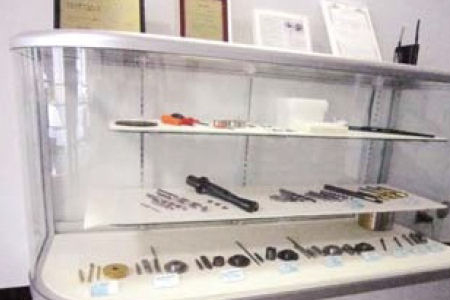
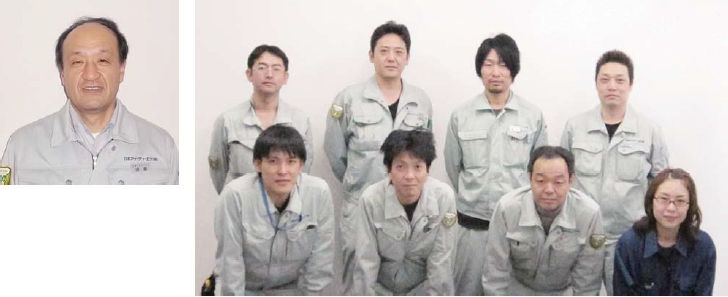
左:久世工場長 田原 三義氏
右:活動事務局、推進リーダーの皆様
後方:左より、片山 鉄也氏、新井 弘樹氏、盛山 英之氏、橋本 弘明氏
後方:左より、土井 一正氏、秋口 英人氏、上西 猛氏、大島 歩美氏
全体最適の実現に向けて
本日はよろしくお願いいたします。まず久世工場の概要についてお話ください。
上西: 当社では主に金属を始めとする様々な材料の表 面処理を行っています。切削工具や自動車のエンジン部品など過酷な使用環境にある製品にコーティングを 行うことで機能性や耐久性を高めることができます。久世工場ではカスタマイズ仕様によるセラミックコー ティングを展開、洗浄から成膜、検査、出荷までの一貫作業を行っております。
活動を開始された動機はどのようなものだったのでしょうか。
上西:
工場長からテクノ経営を紹介されたのがきっか けです。それまでも社内で5S活動や小集団活動などを推進していたのですが、どうしても部門主導で温度 差のある活動になっていました。テクノ経営のセミナーに参加した工場長から、今までの自主活動に一度コ ンサルタントを入れてみてはどうかというお話をいただきました。
工場診断を受け、全体最適を目指す活動をスタートすることにしました。過去の活動ではどうしても役職 者を中心としたメンバーが主体となって進めていましたが、今回のプロジェクトを組むにあたっては工場全 体で取り組むこと、生産だけでなくて事務や営業も含めた全体最適を目指すことにしました。
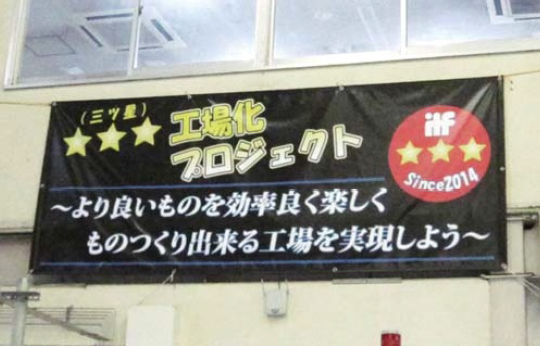
活動の概要をお話ください。
上西:
:「★★★工場化プロジェクト」は久世工場の全体最適を目指す活動です。まず自分たちが「なりたい工場」の姿をえがき、活動のスローガンを決め取組みました。活動期間は2013年10月から1年間の予定で進めました。準備期間を経て、「より良いものを効 率よく、楽しくものつくり出来る工場を実現しよう」をスローガンとして、活動を進めました。
★★★(三ツ星)という名称は、全員からアンケートをとって、その中で選定したものです。またその名称の思 いはお客様から★★★の評価をいただく事と生産を効率化する事により3名の活人化を目指す活動とする事を意味しています。
準備期間はどのように進められましたか。
上西:
最初は何をやっていこうかということで、やはり体制や進め方などを決める必要がありました。そこで活動推進体制として、工場全体の活動とするために 若いメンバーの大島さんと盛山さんに事務局をお願いしました。初めはできるかなという不安なところもあ りましたが、結果的にはよく頑張っていただいたと思います。活動テーマについては少し選定に悩みましたが、コンサルタントにも相談して、3つのステップに分けて1年間のスケジュールを組み目標「3名の活人 化」へ向け活動を展開しました。
第1ステップはレイアウト変更、第2ステップでは品質向上、第3ステップは作業改善としました。最初の テーマは工場レイアウトの変更だったのですが、準備期間での工場の現状調査に関しては事務局も段取りが 大変だったと思います。
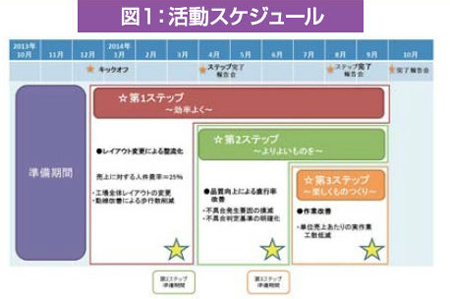
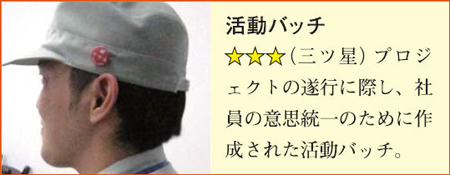
今回、活動事務局を担当された大島さんや盛山さんはいかがですか。
大島: 正直な気持ちとして、最初は嫌だったのですが (笑)。しかし、改善を取り組むなかで、実際に作業をしている人のことを考えながらやることができるよう になりました。そういうところは自分でも少しは成長できたのかなと感じています。
盛山:
最初は単純に「できるのかな」と不安な気持ちでいっぱいでした。役職や年齢も違う皆さんに対して、事務局という形で上手く関わっていけるだろうかと考 えていました。
過去の5S活動などでは、アドバイスをもらいながら自由に活動を進めていたのですが、自分たちで大き な課題を設定した今回の活動はゼロから始める感覚でした。
第1ステップ:レイアウト変更による整流化 ~効率よく~
第1ステップではレイアウト変更にどのように取り組まれましたか。
上西:
第1ステップのレイアウト変更は、効率のよい モノの流し方を討議するなかから出てきたテーマです。活動では、各班のエリア分担を決め、作業台、台車、 棚、設備などのサイズや配置をリスト化して工場レイアウト図面に落とし込んでいきました。
そして、現状を把握するために歩数計を用意して、全従業員の日々の歩数を計測しました。レイアウト改 善にあたっては1歩1秒という指標を用いながら、目標である歩数の半減に向けて進めました。また不用品 は1年ぶりの赤札作戦により撤去、また動線なども調査してレイアウトを大きく変えていきました。
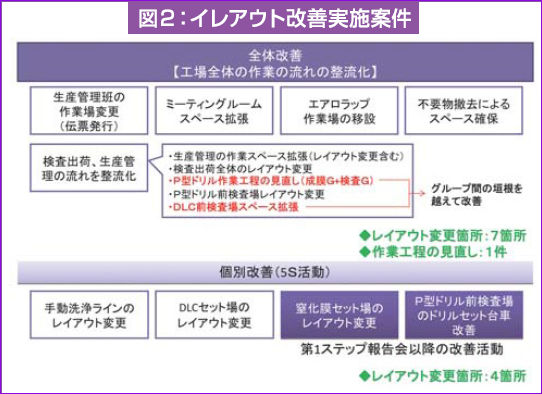
レイアウト変更作業は工場全体で行ったのですが、特に検査部門のレイアウトが大きく変わりました。そ してレイアウト変更の結果、目標の歩数半減には到りませんでしたが、高い歩数削減の成果が生まれました。 各班個別でなく、全体を見渡したなかで考えると偏った動きがなくなりムダが大幅に軽減されたと思います。
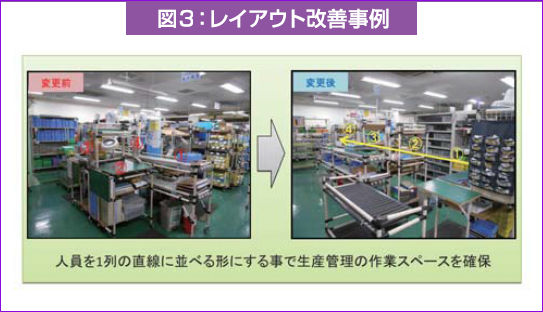
レイアウト改善により、どんなところが変わってきたでしょうか。
上西:
私の個人的な感覚では、成膜や検査部門の職場一帯は非常に狭く思っていました。実際に調査すると複雑でムダな棚も多く、作業環境をさらに手狭にして いました。棚の位置を変更する、あるいは台車化するなど、試行錯誤の改善を続けながらムダな棚や備品類 を整備していきました。今、改めて現場を見るとモノの流れが良くなり、全体が見渡せる状態になりました。ま た出荷場などにも狭い部分がありましたが、それを捻出するために各班が連携して改善を進めていきました。
実際の作業としては、毎週金曜日の終業後に残ってエリアごとにレイアウト変更していきました。ただ一 気にできないので活動が大詰めを迎えた2~3月頃が大変でした。またレイアウト変更は単独の部門だけで は限界がありました。そうしたとき他班のメンバーが協力に来てくれて、みんなの力で変更できたことがよ かったと思います。
秋口: 第1ステップリーダーとしてレイアウト変更を メインに1~3月にかけて作業しましたが、確かに先ほど課長が言われたように、金曜日の遅い時間まで手伝っていただいて助かりました。
片山: レイアウト変更では、改善前の現状把握で図面を見ても狭いというのがわかりました。台車や棚がたくさん有り、その改善には大がかりな工事が必要では という感覚がありました。しかし、それよりもモノを減らして、やり方を変えてという工夫で「場所が広く なる」、「作業がしやすくなる」という方向で改善できてよかったと思います。以前から工場内には縄張り意 識があり、違う目線で物事を見ていたのですが、活動後は人間関係の面でも壁が低くなったように感じます。
第2ステップ:品質向上による直行率改善 ~より良いものを~
第2ステップは品質向上がテーマだったのですか。
上西:
そうですね。レイアウト変更は3か月で終って、 次の第2ステップに進みました。
品質向上のため不良や再加工によるロス削減を目指しました。活動指標としては正規の流れで仕上がる割合を直行率で表し、その数値を低くしている要因を分析し、課題に取り組むことにしました。また目標としては全体の直行率90%以上を目指しました。
ところが、この品質向上というテーマは工場だけでできない部分を含んでいます。当社技術のコアな部分でもあり、技術的な要素が関係しており他部署との連携が欠かせません。そのあたりが難しいところでした。
技術部門と連携して活動することはいままでにもありましたでしょうか。
上西: 個別の連絡会などではありましたが、プロジェ クトとして協力メンバーに加わっていただいたのは初めてです。製造課だけで判断できないこともありますの で、毎回、テーマを宿題として持ち帰ってもらいました。
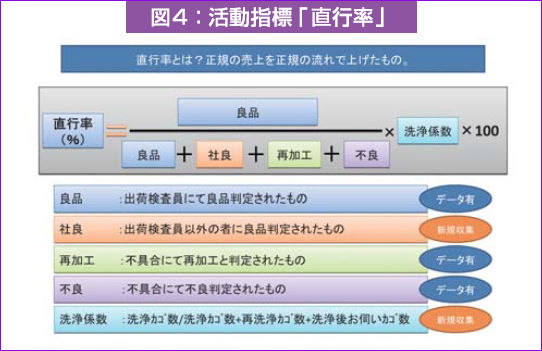
第2ステップリーダーの橋本さんはいかがですか。
橋本:
検査を専門的に携わる者として良いものを出したい気持ちはみんな一緒です。技術課や品質保証Gとは普段からやり取りはしているのですが、活動の協力 により判定基準を明確にしていただき、検査・出荷班の判定スピードもアップしました。
従来のプロジェクトでは特定のメンバーが中心になっていましたが、今回の活動では各部門の主力メンバーがおられたので活動のベクトルが統一されたと思います。
品質向上の活動に取り組まれていかがでしたか。
上西: 今回の活動が終わった段階でアンケートを取っ たのですが。やはり第1ステップのレイアウト変更はやった感、達成感がありました。ところが第2ステップの 品質向上では、まだまだやるべきことがあるという意見がありました。
品質問題はやってもやっても限りないということですね。
上西: そうですね。今回、直行率という指標を用いましたが、再洗浄やコーティングなどの不具合のデータを取っていました。活動を通じて数値はスタート開始 時よりは上がっているのですが、洗浄や検査基準などの技術的な問題、お客様と関わる営業的な問題など、 工場だけでは対応できない課題が多いことがわかりました。目標達成という意味ではまだまだやるべきこと はあると感じています。
ステップ3:作業改善 ~楽しくものつくり~
第3ステップでは作業改善に取り組まれたわけですね。
上西: 第3ステップでは、まずパートさんを含む全員からアンケートを収集しました。その結果300件以上のいろいろな意見が出てきました。これだけの提案 件数が集まったのは、第1・2ステップの成果ではないでしょうか。第3ステップでは、それらを集約して、 優先度の高い21件を取り上げてスタートすることにしました。
集約する作業等で第3ステップリーダーとしてご苦労された点はありますか。
土井: 全部署に回したのでアンケートも相当数集まりました。なかには同じような意見や、グチみたいなことを書いている人もありましたが、それらを一覧表に して絞り込んでいきました。活動期間が3か月と短かったので、効果は期待できるが10月末までに完了できないテーマでは困ります。今後の活動にも役立てるように、効果と達成時間を点数付け、優先順位を決め ました。技術課や品質保証Gを巻き込んで、毎週月曜日に集まり21件の進捗状況を確認する会議を続けていきました。会議は意見を言い合って終わることもありましたが、いい感じのぶつかり合いで、溝ができる ような感じではなく、わきあいあいと進められたのではないかなと思います。あとはパートさんが大変だったのを大島さんが上手くやってくれたと思います。
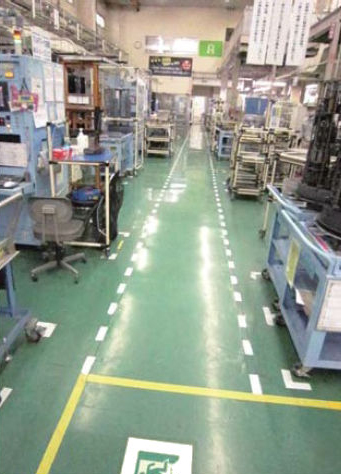
整流化された工場
活動に際してはパートさんからの抵抗があったのでしょうか。
大島: やはり何かを変えるとなったら嫌がる方が多いので、最初は相当な反発がありました。しかし、なぜそうするのかをしっかり説明して、何度も説得して、 今は納得してやってもらっています。少し苦労しましたが(笑)。
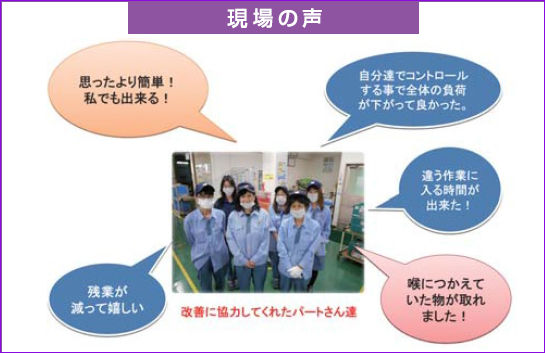
一番気をつかったことは。
大島: レイアウトも作業改善も目に見えて変わっていくので気を遣いました。あとのフォローが大切でした。
新井: 私は協力メンバーという位置づけでしたが、繰り返し説明するなかで逆に希望や積極的な要望が出てきて、結果として良い方向に進んでいきました。
活動成果と苦労したこと
活動を通じた活動成果や自信がついたこと、ご苦労された点などお聴かせください。
土井:
以前にも一度改善を試みてあきらめた案件がア ンケートに出てきていました。それが今回は意外に上手くいって、パートさんにもわかっていただきました。 以前はあきらめていたのですが、もう少し頑張ったら達成できたのかなと思います。
他の案件についても、技術課や品質保証Gと一緒に進められたのが新鮮で、他の人の意見を聴くことで気づきが深まったと感じています。
苦労したことは、時間が短かったこともあるのですが、打合せが終わったとおもったら、もう次の会議が やってくることです。それまでに何か進めないといけないのでプレッシャーを感じていました。通常の業務 だけで手一杯のところを、まだ改善活動が増えているので時間をつくるのがすごく大変でした。
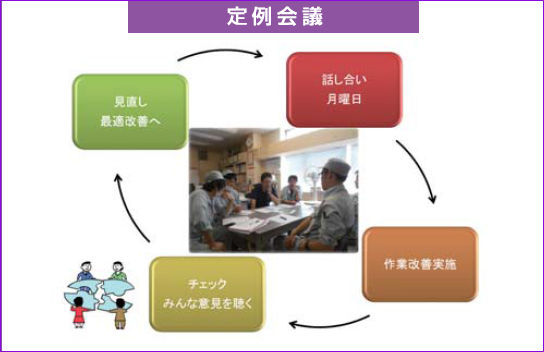
大島:
事務局として苦労した点は、この活動のために 作業から抜けることが多くなったことです。パートさんから「また」とか「何時までいないの」とか結構責められることが多くて、「次はなに」「いらんことせんといてや」と言われたことがあり、それが自分のなかで ストレスになっていました。
最初のレイアウト変更でもそうですが、もともと班の壁は分厚かったのですが、この活動を進めることで お互いの仕事内容とか場所の使い方なども理解でき、お互いが協力できるようになりました。
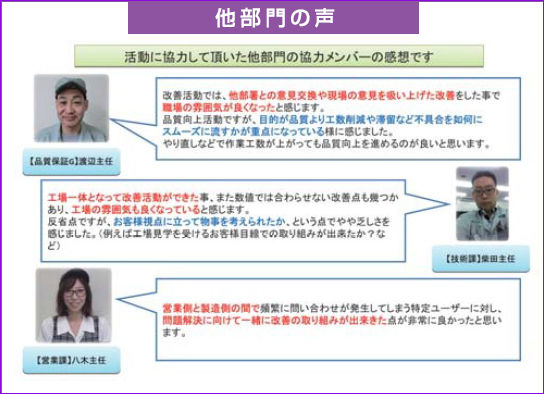
苦労していた部分も活動を続けるうちに自分のメンタルも強くなってきました。そこで対応もいろいろできるようになり、自分自身にとってもよかったなと思っています。
最初は事務局という役割も苦手だったのですが、今後の自主活動でもう一度事務局をと言われたときには すぐに受け入れられる自分になりました。今後も頑張っていきたいと思います。
新井:
過去の5S活動や小集団活動は個別の改善としては結構いい活動だったと思います。ただ、先ほどもお話に出ましたように各部門には縄張りの意識があり 個別最適化が優先され、全体としてはあまり変化がなかったのだと思います。今回の活動で全体最適化を目 指したことで、全員で協力しながらできたことが良かったと思います。
苦労した点は、第2、第3ステップと進むなかで、第1ステップを活動しながら、次の準備も必要になってくるというところで同時進行はなかなか難しいと感じました。
第1、第3ステップでは、やればやるほど成果が目に見えて現れてくるので、そこは活動の楽しみもありますし、みんなが積極的に取り組めるところでした。
反対に第2ステップの品質向上は目に見えてすぐに効果が現れるものではないので、活動の実感が薄いのが難点でしたが部門を越えた活動が進められたので結果としていい方向に向かっていると思います。
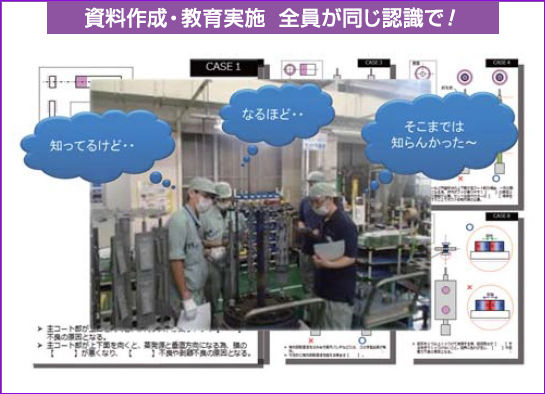
盛山:
3ステップの個々の活動は短かったのですが、 1年間という期間を気持ちを切らさずに継続して頑張れたので良かったと思います。
また自班内だけの活動ではなく、他班・他部門と協力して活動に取り組めたことは良かったです。
事務局としてのポイントは、スタート時に「なりたい工場」の姿をきちんと最後までイメージしながらメ ンバー全員をサポート出来たかどうかです。
短期的に目標を揚げ活動するので、1年間を通じて見るとどうしても理想とのずれが生じるのかなと感じ る事も有りました。限られた時間の中で急がされる様な活動になってしまい、納得のいく形にならず進んで しまった事も有ったと思います。
そういった部分を反省点として受け止め糧とし、今後も良い活動になる様にしていきたいです。
橋本:
実はレイアウト変更に関しても、もう数年も前からやっていて、座って検査をしているところを立ち作業化するなど進めていました。その当時はパートさ んなどの作業者にも通達なく、勝手に週末に入れ替えたりとかしていましたので、大島さんが苦労されたような反発がありました。今回の活動でのパートさんの反発の背景には、恐らくその当時のやり方に対する不 満があったのかなと思います。
今回は準備期間を設けて、コンサルタントからも手法を指導していただきながらスタートが切れたので、 ある意味で苦労はありましたが、事前に班員の協力や理解を得ながら進めることができたと思います。
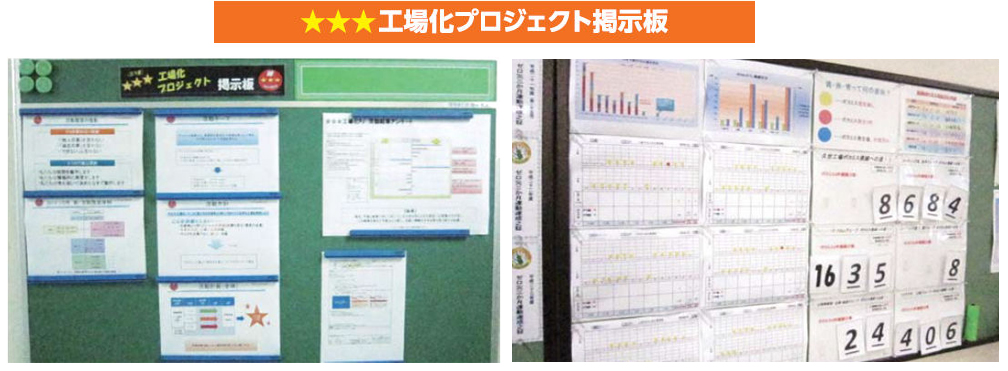
上西:
忙しい作業のなかで1週間に1回べったり活動をやっていたので、みんな厳しかったと思います。みんな通常の作業があるなかで時間を捻出していました。 会議も含めて、通常業務のなかで活動をしていたので大変だったと思います。そういった環境のなかで各メ ンバーに地力がついてきたと感じています。
コンサルタントがいることでやらなければという思いがでてくる。そういう効果はあるのですが、それ以上にいろいろな改善手法などを教わって、若いメンバーにも身に付いてきたと思います。事務局をやってもらった大島さんと盛山さんも、そういった立場にないとすれば抵抗に回る側だったと思うのですが、もう今はリーダーとして逆の立場になっています。昔の自分を思い出す部分もあるかもしれませんが(笑)。立場が変われば現状の若いメンバーを成長させていくためには、自分も成長しなければと思います。そういう意味ではいい経験になったかなと思います。
事務局を経験すると180度見方が変わるでしょうね。 上西課長が一番ご苦労なされた点はなんでしょうか。
上西:
工場長のプレッシャーですね(笑)。やはり経営的に見れば投資効果を考えてしまいます。売上が増えても人員補充もなくやっていけていますので、数字的には3名の活人化が達成でき、会社として満足してもらっていると思います。
アンケートでも「楽しく」というところを重点においていたが、まだまだ不十分な結果でした。やはりこうした改善活動はどうやったら楽しめるのかなという、私はいつも疑問に思うのですが(笑)。そこが難しい ところですね。
今後に向けた活動やビジョンをお聴かせください。
田原:
今回の活動では、プロジェクトメンバー全員が、 よく考え、積極的に行動してくれたことにより、工場全体が活性化し、目標に掲げた「なりたい工場」と「3 名の活人化」の実現に近づいてきたと思います。また、今回の活動により、メンバーたちのなかに、自分達の工場を「力を合わせ、良くして行こう」という自覚が芽生えたと確信しています。
ただ、厳しい見方をすれば、現在の活動は工場及び関係部署を巻き込んだ、全員参加の活動という意味で は、まだまだ完璧とは言えません。今後の自主活動では、久世工場全体での、目標を共有化し、全員で成果を出し、達成感と歓びを分かち合ってもらいたいと思っています。
上西:
これからは自主活動になりますので、この1年間の活動でやり残したことも含め生産効率を上げていきたいと思います。
2015年の目標に向かって、受注増により作業量も増えることが予想されますが、人員増を必要最小限 に抑えつつ、「歩行数」「直行率」「売上百万円あたりの実作業時間」等の指標も有効に活用しながら現在抱えている問題を工場全体で改善し、「なりたい工場」を達成すべく活動を進めていきたいと考えています。
田原:
私は企業の評価というものは、お客様や外部の 方々からいただくものだと考えています。自社の強みを敢えて言うならば、他社に勝る独自の薄膜技術を追究し続けていること、そしてお客様の多様なニーズに合わせた対応ができることではないでしょうか。
将来に向けたビジョンとしては、売上や利益の目標達成は当然として、何よりもお客様に喜ばれる商品・ サービスを提供し社会に貢献することを目指したい。そのためにも社員の一人ひとりが生き生きと歓びを持っ て「楽しく」働ける会社にして行きたいと考えています。