本ページでは、三和ハイドロテック株式会社様に対するコンサルティング実績をご紹介しています。
私たちの生活にはポンプの存在が欠かせない。生活用水や農業用水の運搬はもとより、自動車や電車などの装置にもポンプが使われている。 また、工業界でも、石油、化学、製薬、食品など幅広い産業分野で様々な用途のポンプが活躍を続けている。そんなポンプ業界で、独自の 技術力とアイデアで勝負する企業が三和ハイドロテック株式会社である。
創業80年に及ぶ社歴、日本初の高級ステンレス鋳鋼で培われた伝統を活かした、オールステンレス製のサンワマグネットポンプは、漏れない・安全性・信頼性・長寿命などの品質が世界で認められ、国内外の幅広い産業分野で活用されている。食品・製薬向けに外気と機内を 完全にセパレート、異物混入を防止するサニタリーマグネットポンプは業界初の新製品。毎日の分解洗浄が容易にできる高いメンテナンス 作業性を持つ。
同社では、5S定着と人材育成を目的に7年前にVPM活動を導入、現在は社内での自主改善を推進中である。
(※ASAP 2013年 No.3より抜粋)
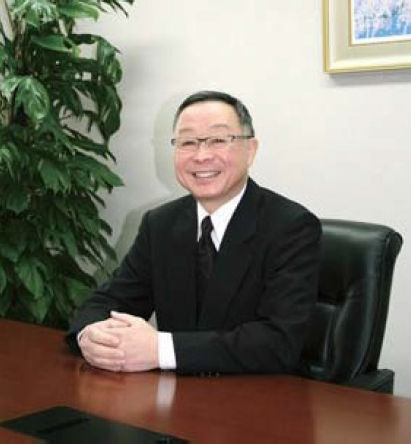
三和ハイドロテック株式会社
代表取締役 堀内 清隆 氏
きっかけは関連企業の工場移転
本日はよろしくお願い申し上げます。最初にコンサルティングご導入の経緯についてお伺いします。
堀内:
約8年前、関連企業の日本コーディング株式会社が工場移転を予定していました。当時(2005年)、 東京工場が騒音や粉塵の問題で街中での操業の限界を迎えており、新たな工場候補地への移転が急務となっていたのです。工場移転に関しては、当社(三和ハイ ドロテック(株))でも過去に工場を尼崎市から京都府福知山市に移転した経験があります。しかし、そのときは計画や準備段取りの一切を自力で行ったため非常に 苦労しました。それで、今回の移転については外部の専門家にアドバイスをお願いする必要性を感じていました。
ちょうどその頃、知人の紹介で、テクノ経営総合研究所のセミナーに参加する機会がありました。お話を伺えば製造業の幅広いテーマに対応できるとのこと。そ こで、関連会社の工場移転プロジェクトをお任せすることにしたわけです。また、それと並行して、当社の大阪工場と赤穂工場でもコンサルティングをお願いすることにしました。
工場レイアウト改善で生産性アップ
工場移転プロジェクトは順調に進んだのでしょうか。
堀内:
工場移転プロジェクトは、まず工場立地の選択から始まりました。コンサルタントのアドバイスを受 けながら、複数の候補地からしぼりこんでいきます。そして、最終的に埼玉県行田市にある工業団地に決めました。最寄り駅から遠く徒歩30分程度かかります が、特急が停車するメリットがあったためです。
工場の移転計画は準備も含め約1年かかりましたが、引越しの段取りも指導いただきスムーズに進行できま した。仮に自力でやったら大混乱しただろうと思います。やはり専門家に任せてよかったと思いました。また、工場移転のプロセスで関連企業の人材も成長しま した。
今回取組まれた活動の概要をお聞かせください。
堀内: 第1期活動(2006年3月~2007年3月)が大阪工場(本社)と赤穂工場、第2期活動(2007 年4月~2008年3月)は京都工場で推進しました。活動目的は、5S定着と人材育成が主な内容です。約25年前から社内で実施している5S活動ですが、外見的には綺麗だが、本質的な理解が不足していると感じました。活動を通じて職場リーダー育成をはかり、自主改善の定着を目指すことにしました。
活動前の工場診断はいかがでしたか。
堀内:
「クレーン速度に合わせて動くムダ」――これが工場診断における最初の指摘です。当社の前身は鋳 物工場、そのため運搬はクレーン中心でした。そして、業態が変わっても何の疑いもなくクレーンに頼っていたのです。
工場診断を受けてよかったことは、外部の視点で当社の現状を評価してもらえたことです。工場診断という形で専門家の意見を伺うと、新たな気づきが数多くあ りました。
そうした課題にどのように取組まれたのでしょうか。
堀内:
その対策として実施したことの一つが工場レイアウトの検討です。コンサルタントの指導のもと、工 場図面を壁に張り出し、設備や機械の位置にピンを打ち、その間をヒモで結びながら動線分析を行いました。この工場レイアウト改善という発想は社内からは出て こないアイデアでした。それだけに新鮮に受け止められたのではないでしょうか。
この検討の過程から、今までクレーンに頼っていた運搬を台車に変更するという 新たな発想が生まれてきました。クレーン速度は一定のため改善余地がありませんが、台車なら動線と作業の工夫でムダな時間や距離も削減できます。また、それ までは大型の作業台で組立等の作業を行っていましたが、IEによる作業分析を実施し、小型の屋台形式の作業台に変更することで作業効率が改善されました。その 後も、当社では“一歩一秒一円”の思想で作業改善を続けています。
全体の活動を通じた成果はいかがでしょうか。
堀内: 社内で実施していたときとは違い、プロの指導を受けたことで5Sの本質がつかめてきたと感じています。また、リーダー育成も達成でき、大きな成果があったと思います。
フォローアップで自主改善の定着をはかる
コンサルティング終了後の自主改善は順調でしょうか。
堀内:
コンサルタントが去ったあと、せっかくの改善成果がもとの木阿弥になる企業も多いと聞きます。当社では、コンサルティング終了後も現在まで自主改善を続けてきましたが、この5年間で活動の目処が立つようになったと自負しています。
現在取組んでいる新しい課題が在庫削減です。当社の在庫状況に関しては、リーマンショック後の受注減で在庫量も減少しましたが、翌年の尖閣諸島問題で日中 関係が悪化、希土類製品の供給制限が予想されました。マグネットポンプが主力製品の当社にとって、部品供給が途絶えると大変。少なくとも1年間の備蓄は必要 と考えました。また、2011年には東日本大震災が発生。震災後はポンプ受注が急増したため、在庫量を一挙に増加させる必要性が出てきました。その結果、 現在も在庫過剰の状況が続いているからです。
なんとか社内の改善意識で引っ張っても、4~5年も経つと次第に5Sに乱れが出くるものです。当社でも、 この在庫や新入社員のレベルアップ等の必要性もあり、コンサルティング後もフォローアップをお願いしている次第です。
創業者の想いを継承する
将来のビジョンについてお話ください。
堀内:
当社独自の強みは、マグネットポンプをステンレス、チタン、ニッケル、タンタルなどの素材で製造できることです。海外の顧客はアメリカ、中国、台湾など、競合メーカーはヨーロッパ、アメリカが中心になります。
今後の方針としては、石油化学系、 リチウムイオン電池、LED、ポリカーボネイト、炭素繊維など、新分野の顧客開拓を強化することです。例えば、食品用のサニタリーポンプは専門メーカーと 共同開発し、2011年に製造・販売を開始しました。まだ普及途中の段階ですが、当社のマグネットポンプ技術を活かした製品となっています。
ステンレ ス鋳物を日本で初めて製造したのが当社です。その経緯を活かしてバルブやポンプ製造専業に転身したのが10年前です。それまではステンレス耐熱鋼の製造も 行っていましたが、中国などからも安価な製品が出回るようになりました。
創業の事業をやめるにあたって、最後の鋳込みで数十個のエンブレムをつくりま した。そして、№001は創業者の仏壇にささげています。創業者の想いをエンブレムに「新技術 新素材 新製品」という言葉で刻んでいます。この言葉の意味は、 「常に変化を続ける世の中で、その時その時、世の中の役に立つものを生みだして、提供することでお客さまに喜んでいただこう、評価していただこう」という ものです。それを続けることが我々の世の中への貢献になる。それが勝ち残り生き残る原理であると思います。当社は来年80周年を迎えますが、これからもこの路線を歩んでいきます。
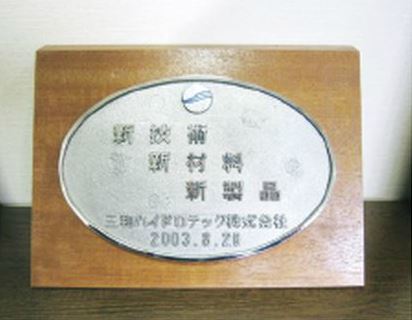
VPM活動事務局の苦労話
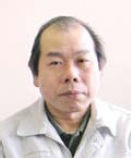
三和ハイドロテック株式会社
京都工場 工場長 小野 裕嗣 氏
京都工場での活動開始時、私は生産企画や工程管理の仕事をしていました。それまでトヨタ生産方式やJIT、5Sなど改善に関しては 相当勉強をしてきましたが、今になって考えればテクノ経営による工場診断には気づかされる部分が多かったと思います。ちなみに当社では、VPM活動という名称 で通しています。本来は独自の活動名を考える場合が多いと思いますが、当初からVPM活動で通用していましたので、今でもそのままです。
やはり慣れ親しん だ環境にいると気づかないもので、それが当たり前になってしまうと、新たな発想がでてきません。コンサルタント導入に対する社内の反応については、最初は少し 面倒だなという感じはありましたが、現場の反発は特になかったです。各メンバーがコンサルタントを上手く活用することで成長がはかれたのではないでしょうか。
最近は自主改善を主体に、フォローアップとして時々コンサルタントに来ていただいています。5Sとは綺麗にすることだと勘違いしている若手層も、教えてもらっ てはじめてその意味が理解できます。5Sが乱れてきたということもあり、この辺でネジを巻かないとダメだと思っています。コンサルティングと自主改善を繰り返 し、ときどきフォローアップをはさむ方法が長く改善を続けるコツなのかもしれません。
やれといわれたらやるのですが、時間が経つと必ずどこかでだらける。 継続は力なりで続けるが、「明日やったらいいや」となるとだらけるわけです。そこをどうやっていくかが今後の課題です。いろんなことを試しながらやってみたいと考えています。
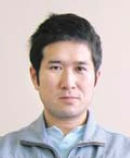
三和ハイドロテック株式会社
京都工場 製造課・資材課 課長 森永 康嗣 氏
私は京都工場でVPM活動事務局を担当しました。当時、ちょうど品質管理から製造に異動した頃でしたが、ルーチン業務をまだ持っておらず活動自体の負担はあまり感じませんでした。全体の生産性向上は、VPM活動だけでなく、様々な要因が重なって実現でき ることだと思います。
ただ、VPM活動は人間育成という面で、今まで与えられた仕事や標準作業だけをこなしてきた人が自分の業務以外にも眼を向ける機会になっ てよかったと思います。本活動はそういった意味での成果の方が大きかったのではないでしょうか。他部門のやり方に学ぶということ、あの人はあんなことをしていると いう気づき。自分自身の誤りに気づいた人もいれば、改善意欲を高めた人もいます。
コンサルタントからは、いろいろな改善方法を習いましたが、重要なことは「自 ら考える」ということだと思います。コンサルタントに言われたからやるではなく、自分から進んで問題に取り組んでみる。そうすることでますます自分自身でやらざる を得ないという思いになりました。それが自己の成長につながった面も多いと感じます。
コンサルタントに指示を仰ぐ状態から、今の作業よりもう一段高い見方をし ようという自主性へ。現在のグループ活動では周囲に対する関心もメンバーの中に芽生えてきました。5Sも工場全体のスケールで見ると成長につながると思います。

三和ハイドロテック株式会社 京都工場様